A sliding window track is the groove or rail installed along the bottom and top edges of a sliding window. It allows the window sash to glide effortlessly, enabling easy operation. Typically, the track is designed to support smooth movement, withstand wear, and resist environmental elements. The plastic profile extrusion process is the preferred manufacturing method for producing these tracks, as it allows for precise dimensions, long-lasting durability, and customization to fit various window designs.
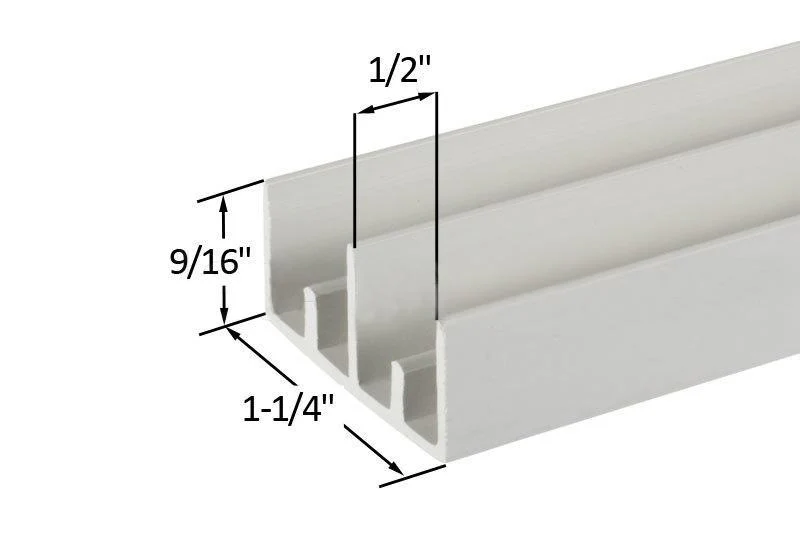
Key Benefits of Plastic Profile Extrusion for Sliding Window Tracks
Using plastic profile extrusion to create sliding window tracks offers numerous advantages, including:
- High Durability: Extruded plastic tracks are resistant to moisture, UV rays, and extreme temperatures, ensuring long-term performance.
- Smooth Operation: The precision of the extrusion process creates smooth, even tracks that allow for effortless sliding of window sashes.
- Low Maintenance: Unlike metal tracks, plastic sliding window tracks do not rust or corrode, requiring minimal upkeep over time.
- Cost-Effective: Plastic is a more affordable material compared to metals like aluminum or steel, making it a budget-friendly option without sacrificing quality.
- Customization: The extrusion process allows manufacturers to produce sliding window tracks in various shapes, sizes, and finishes, making them suitable for different window systems and aesthetic preferences.
The Plastic Profile Extrusion Process for Sliding Window Tracks
The plastic profile extrusion process is key to producing sliding window tracks that are durable, functional, and customizable. Below is a step-by-step look at how the extrusion process works for sliding window track manufacturing:
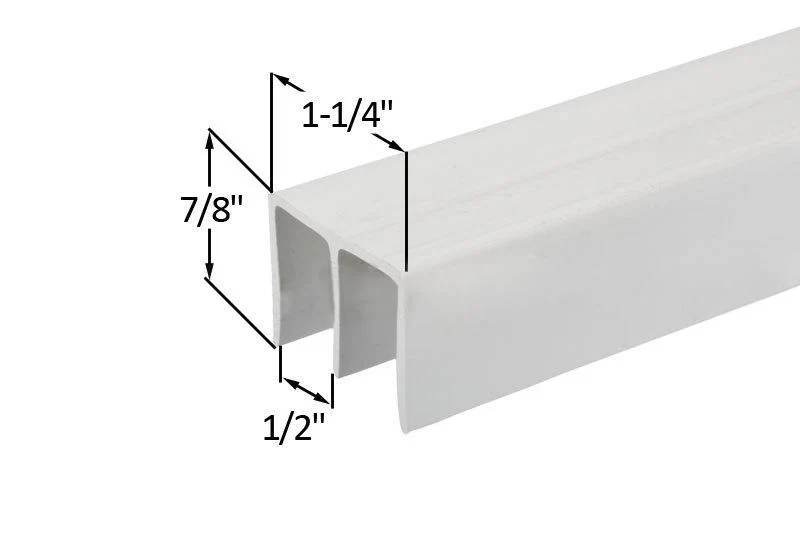
1. Material Selection
The process begins with the selection of high-quality plastic materials, such as PVC (Polyvinyl Chloride) or polypropylene, which are known for their durability and weather-resistant properties. These materials are combined with additives to enhance their performance, such as UV stabilizers and impact modifiers.
2. Extrusion Process
Once the materials are prepared, they are heated and fed into the extrusion machine. The molten plastic is pushed through a die that is specifically designed to shape the sliding window track profile. The die creates the precise dimensions and grooves needed for smooth window operation.
3. Cooling
After extrusion, the plastic profile is cooled to harden it and retain its shape. This step is crucial for ensuring the track remains consistent in size and form, allowing for accurate window installation.
4. Cutting and Finishing
Once the track has cooled and solidified, it is cut to the desired lengths for installation. This process can be adjusted depending on the specific needs of different window systems. Additional finishing steps, such as adding surface textures or coatings, may be performed to improve aesthetics and functionality.
5. Quality Control
Every sliding window track undergoes a thorough inspection to ensure it meets the required quality standards. This includes checking the dimensions, surface finish, and performance capabilities to guarantee that the track functions smoothly and lasts for years.
Why Plastic Sliding Window Tracks are Ideal for Residential and Commercial Use
Sliding window tracks made through plastic profile extrusion offer the perfect balance of durability, functionality, and affordability. Here’s why they are an excellent choice for both residential and commercial applications:
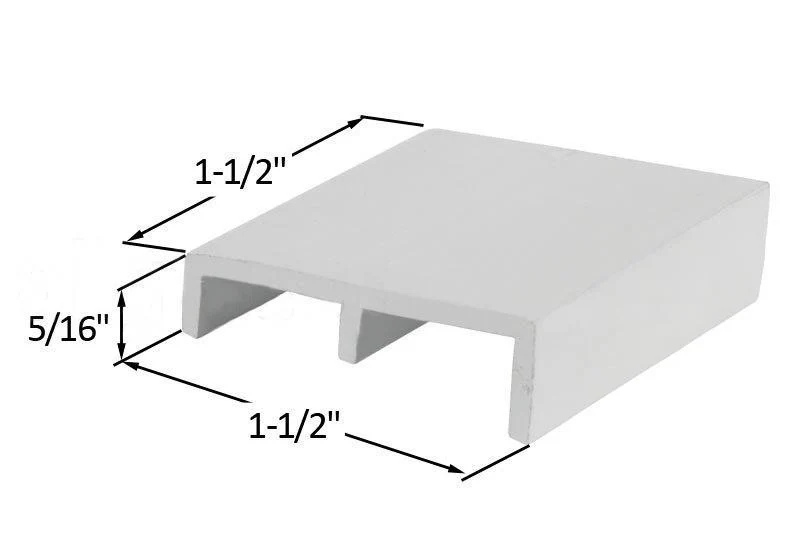
- Weather Resistance: Plastic materials like PVC are naturally resistant to moisture, UV rays, and temperature fluctuations, making them ideal for windows exposed to the elements.
- Smooth Functionality: The precision of the extrusion process ensures that the window track maintains a smooth surface, reducing friction and allowing for easy sliding.
- Lightweight and Strong: Plastic sliding window tracks are lightweight yet strong, offering a high load-bearing capacity without adding excessive weight to the window system.
- Corrosion-Free: Unlike metal window tracks, plastic tracks will not corrode over time, reducing the need for frequent maintenance or replacement.
- Customizable Designs: Extrusion allows for creating custom profiles that meet specific design and functionality requirements, offering versatility in window installation.
Energy Efficiency and Plastic Sliding Window Tracks
Sliding window tracks made from plastic materials contribute to the overall energy efficiency of a building. By providing a tight seal when windows are closed, these tracks help prevent air leakage, which can improve insulation and reduce heating and cooling costs. Additionally, plastic window tracks do not conduct heat as much as metal tracks, further enhancing the energy efficiency of the window system.
Environmental Benefits of Plastic Sliding Window Tracks
In addition to offering practical advantages, plastic sliding window tracks also provide environmental benefits:
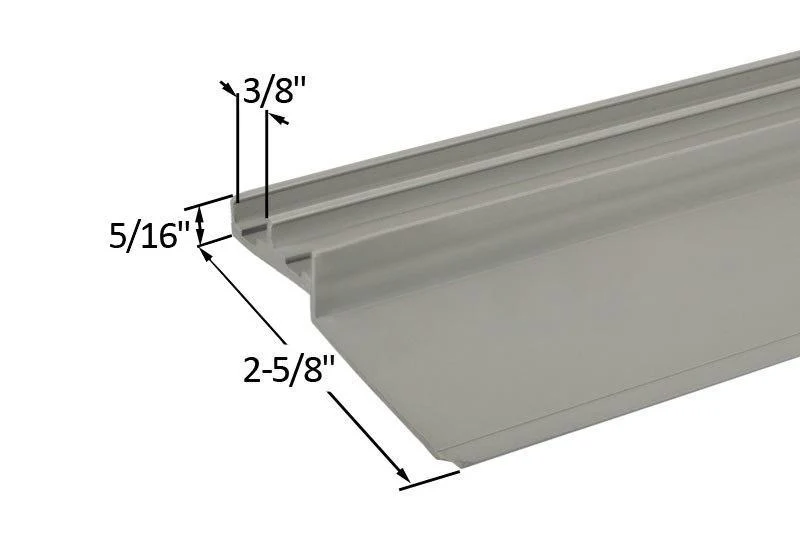
- Recyclability: Many plastic materials used in window tracks, such as PVC, are recyclable. Manufacturers can often reuse leftover material from the extrusion process, reducing waste.
- Sustainable Production: The plastic profile extrusion process is energy-efficient, minimizing energy consumption during manufacturing.
- Longevity: The durability of plastic window tracks ensures a longer lifespan, reducing the frequency of replacements and conserving resources.
Conclusion: The Importance of Plastic Profile Extrusion for Sliding Window Tracks
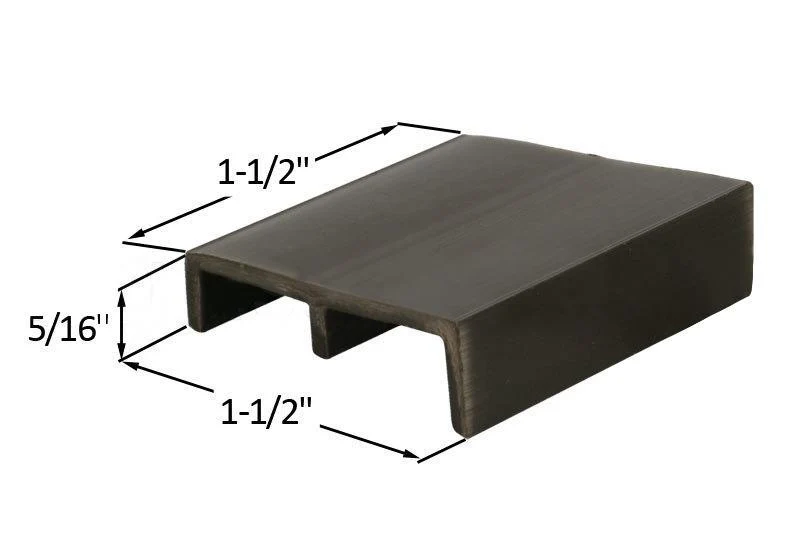
The plastic profile extrusion process is the ideal method for manufacturing sliding window tracks due to its precision, efficiency, and ability to create durable, low-maintenance components. Sliding window tracks made from plastic materials like PVC provide excellent weather resistance, smooth operation, and enhanced energy efficiency. They are also highly customizable, making them suitable for various window systems and design preferences.