The lighting industry demands precision, durability, and cost-effective solutions to create lighting fixtures that meet modern design and performance standards. Plastic extrusion for lighting has become a go-to method for manufacturers to produce customized plastic profiles, diffusers, and housings that enhance both the aesthetic and functional aspects of lighting products.
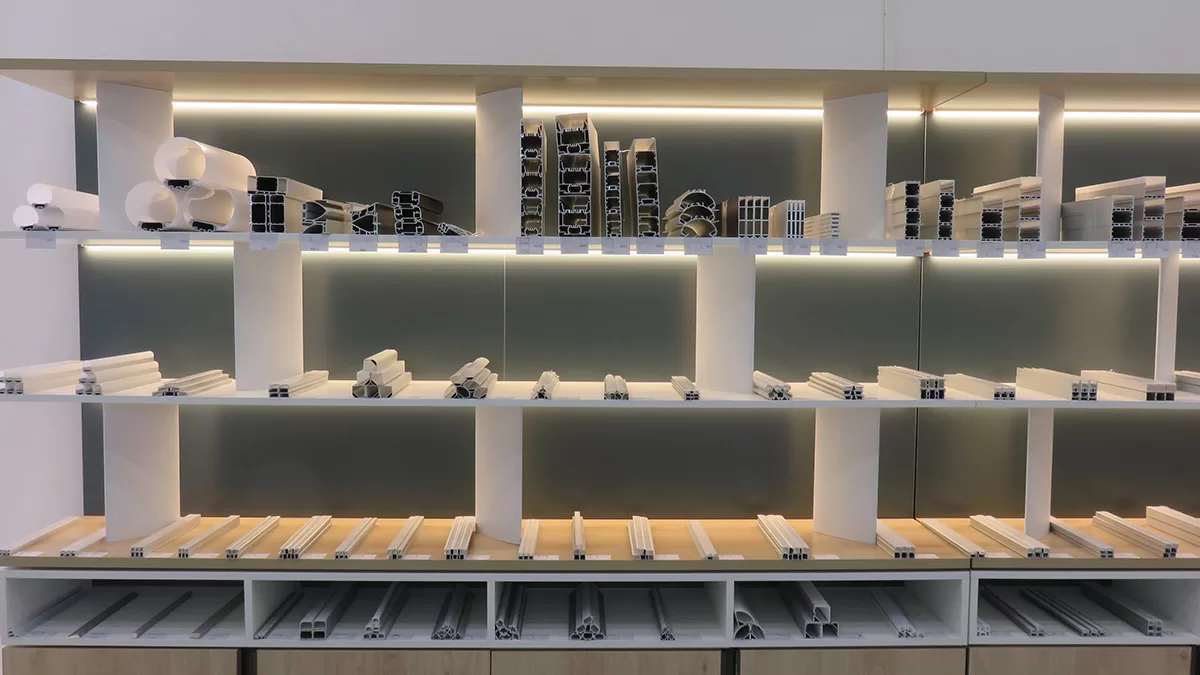
Why Plastic Extrusion is Ideal for the Lighting Industry
The plastic extrusion process involves melting thermoplastic materials and shaping them into continuous profiles through a custom die. This method allows manufacturers to create precise, consistent, and high-quality components suitable for a wide range of lighting applications, including:
- Commercial lighting fixtures
- Residential lighting
- LED strips and diffusers
- Architectural lighting
- Industrial lighting
Benefits of Plastic Extrusion in Lighting
- Custom Profiles
With plastic extrusion, manufacturers can create complex, custom profiles to meet the specific needs of lighting designers and engineers. Whether it’s sleek, linear designs for LED strips or more intricate diffuser shapes, plastic extrusion ensures the flexibility to produce virtually any shape. - Lightweight & Durable
Extruded plastic components are lightweight yet durable, making them easy to handle and install while maintaining long-lasting performance. This is especially important for lighting applications where weight savings can reduce overall installation costs and improve energy efficiency. - Optical Clarity
For lighting, optical performance is critical. Materials like acrylic and polycarbonate used in plastic extrusion offer excellent optical clarity, making them ideal for light diffusers and lenses. These materials enhance light diffusion, reduce glare, and ensure even distribution of light across the desired surface. - Cost-Effective Production
Compared to other manufacturing methods like injection molding, plastic extrusion for lighting is more cost-effective, especially for long, continuous profiles. This makes it a preferred solution for large-scale production runs. - Versatile Finishing Options
Plastic extrusion allows for a variety of finishes, including smooth, textured, or frosted surfaces. These finishing options can enhance the aesthetic appeal and functionality of lighting products, offering both decorative and practical solutions.
Materials Used in Plastic Extrusion for Lighting
Choosing the right material is crucial for the success of any lighting project. Common thermoplastics used in plastic extrusion lighting include:
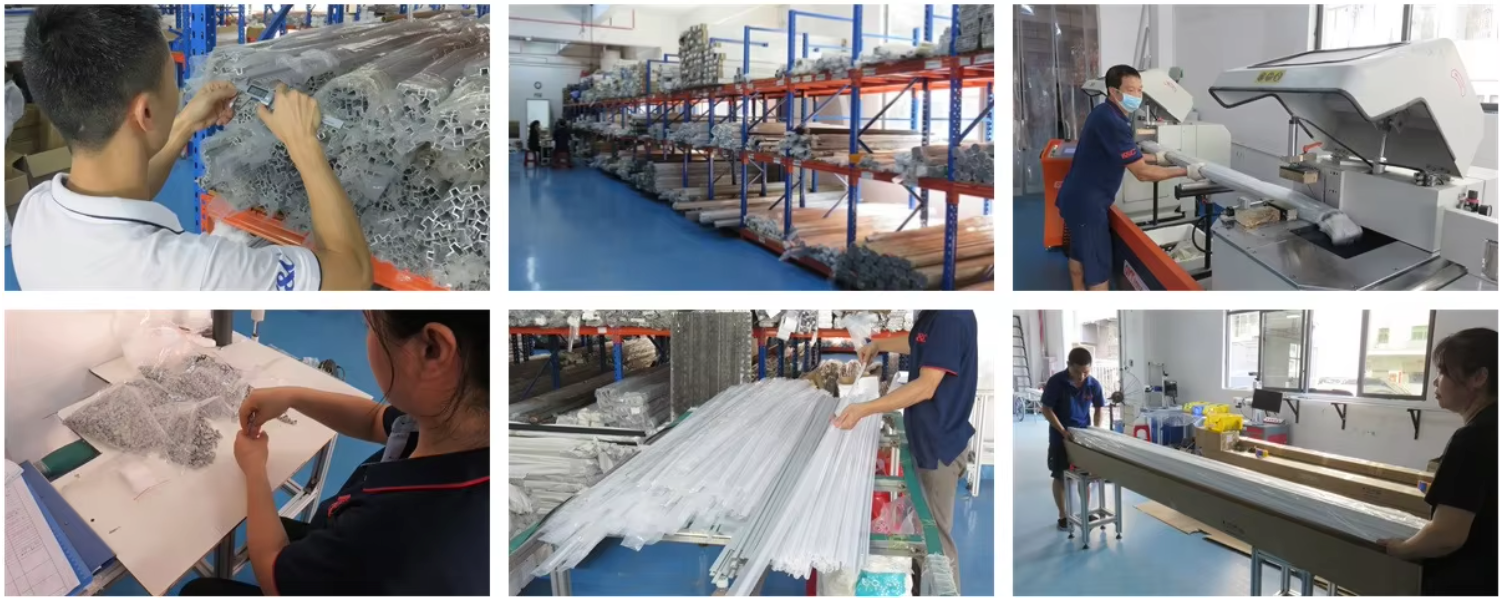
1. Acrylic (PMMA)
Acrylic is known for its superior optical clarity and light transmission, making it ideal for light diffusers and lenses in lighting applications. It’s highly transparent and allows for excellent light diffusion while maintaining durability.
2. Polycarbonate (PC)
Polycarbonate is another popular material for lighting components due to its impact resistance and high-temperature tolerance. It’s commonly used for applications where strength and durability are important, such as industrial lighting and protective covers.
3. PVC
PVC is a cost-effective material that offers versatility and durability. It’s used in the lighting industry for components like cable management profiles, conduit, and protective casings.
4. ABS
ABS is often used in extruded plastic lighting housings due to its toughness and resistance to impact, heat, and chemicals. It’s perfect for outdoor and industrial lighting applications where durability is a priority.
Common Applications of Plastic Extrusion in Lighting
Plastic extrusion plays a key role in creating various lighting components that enhance both functionality and design. Here are some of the most common applications in the lighting industry:
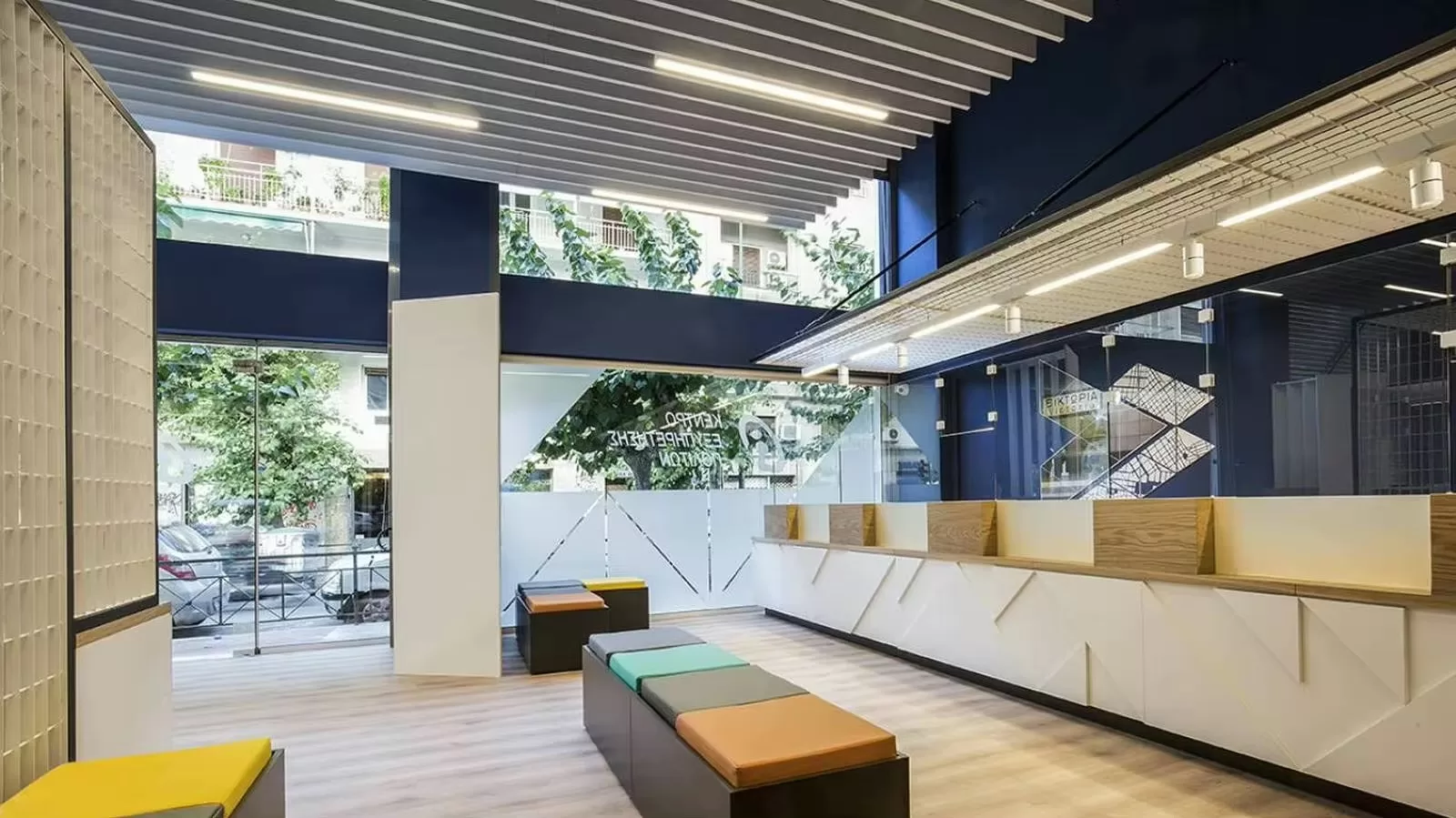
1. LED Diffusers
Extruded plastic diffusers are essential for modern LED lighting. They help to spread light evenly, reduce glare, and enhance the overall aesthetic of lighting fixtures. Acrylic and polycarbonate diffusers are commonly used for their optical clarity and light-diffusing properties.
2. Light Covers and Lenses
Custom plastic extrusions are used to create covers and lenses that protect lighting components while ensuring optimal light output. These covers can be clear or frosted depending on the lighting application.
3. Housing and Enclosures
Extruded plastic is perfect for creating protective housings and enclosures for lighting fixtures. These components are lightweight, durable, and can be customized to meet the exact specifications of the project.
4. Reflectors and Baffles
Reflectors and baffles play a critical role in directing and controlling the distribution of light. Plastic extrusion enables the production of these components with precise geometries to ensure optimal light reflection and control.
Why Choose Plastic Extrusion for Lighting?
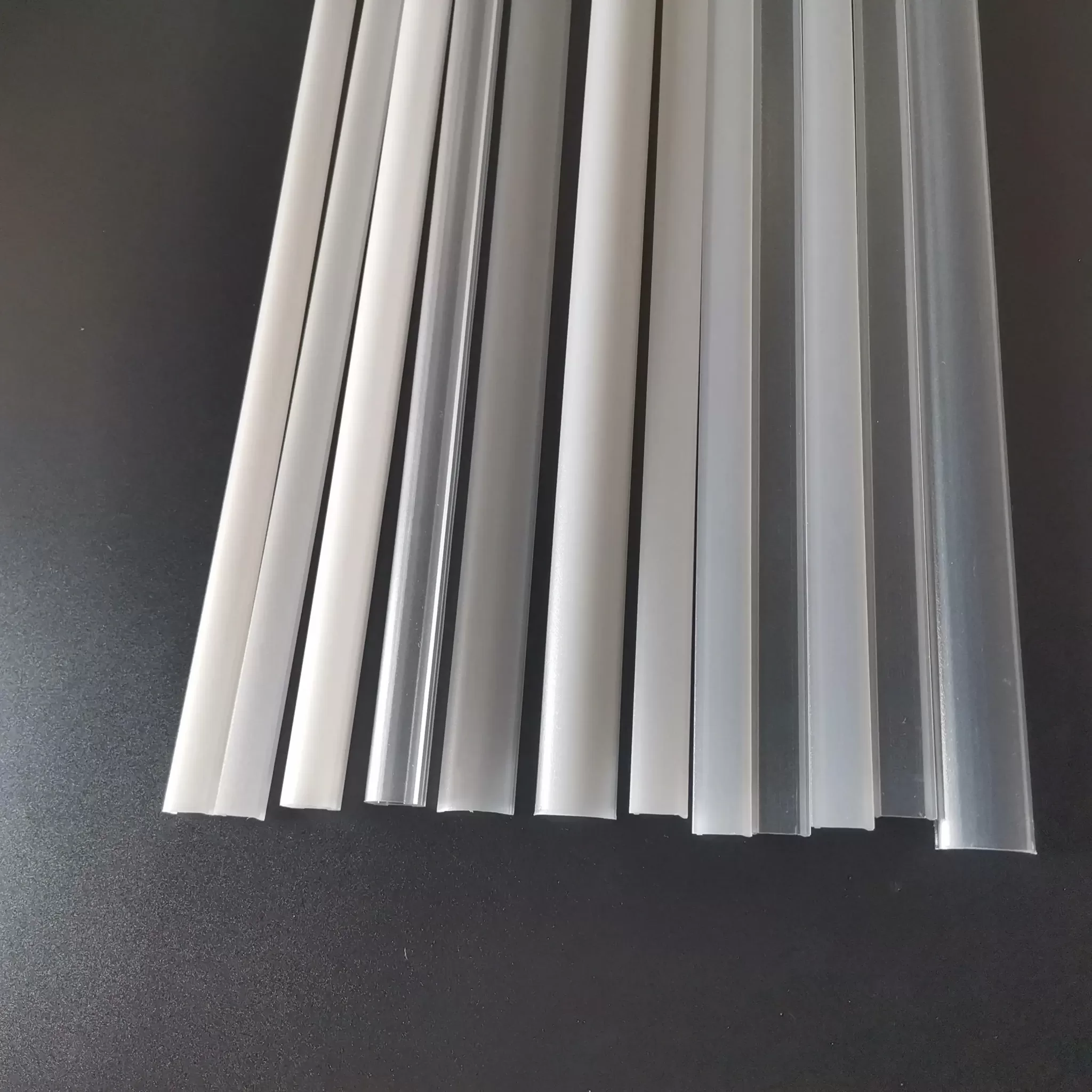
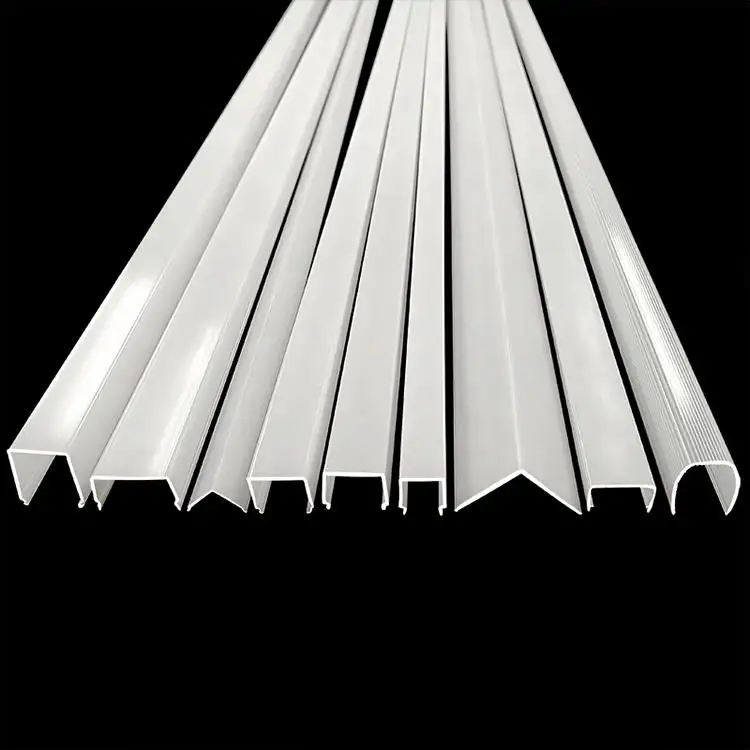
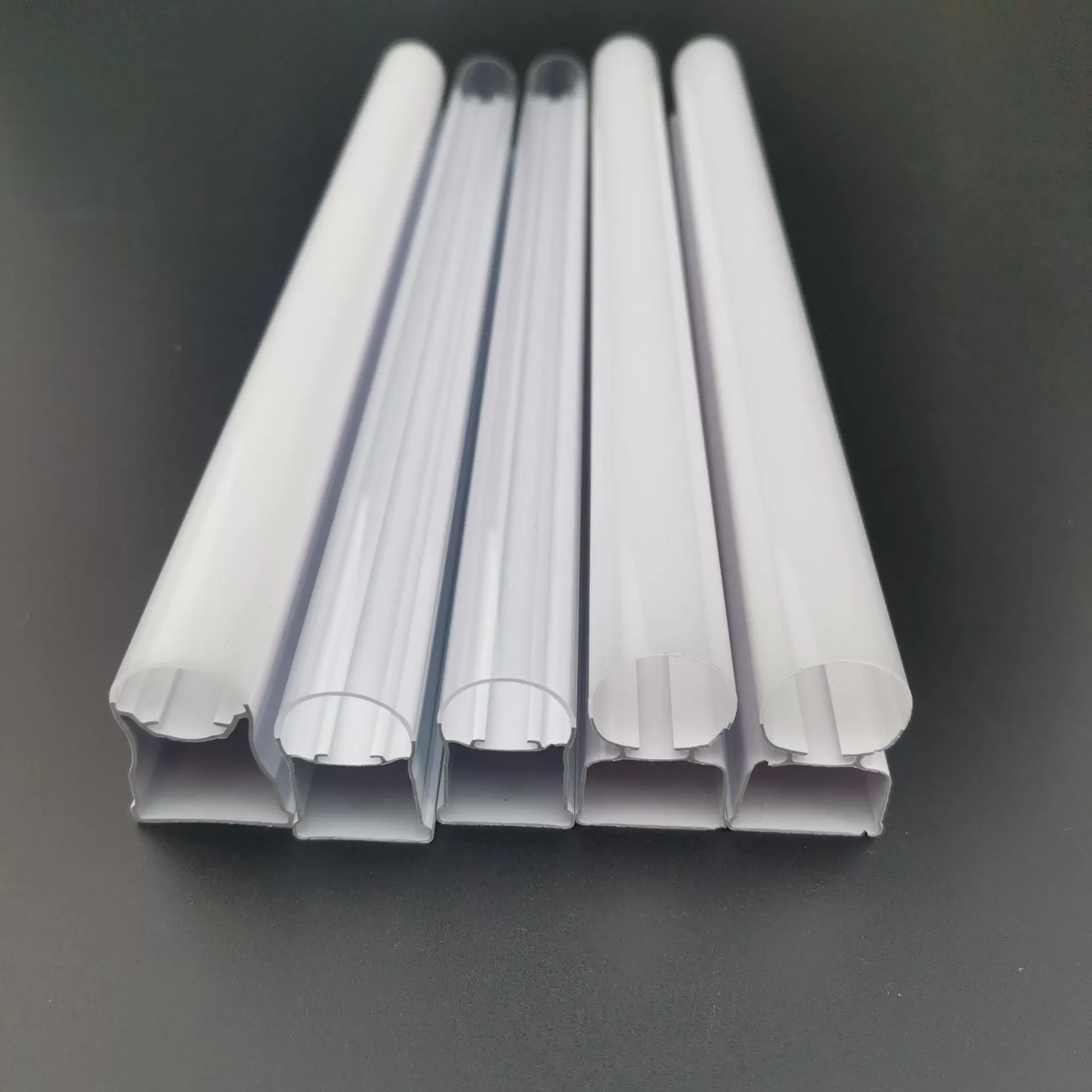
Using plastic extrusion lighting offers several key advantages over other manufacturing processes. It provides a perfect balance between customization, quality, and cost-efficiency, making it an ideal choice for the competitive lighting industry. Manufacturers can create components that meet exact specifications while keeping production costs in check.
Moreover, with the ability to produce both simple and complex profiles, plastic extrusion allows for innovative designs that are lightweight, durable, and visually appealing.
Conclusion: The Future of Plastic Extrusion in Lighting
The role of plastic extrusion for lighting continues to grow as the demand for energy-efficient, aesthetically pleasing, and functional lighting solutions increases. By leveraging advanced plastic extrusion technologies, lighting manufacturers can produce high-quality components that improve both the form and function of modern lighting products.
For companies looking to innovate in the lighting sector, plastic extrusion is a proven method that delivers exceptional results, from light diffusers and covers to housings and enclosures. Choose the right plastic extrusion partner, and take your lighting products to the next level.