Custom plastic rod and tube extrusion is a manufacturing process that has gained popularity across various industries due to its versatility and efficiency. This technique enables the production of a wide range of plastic shapes tailored to specific requirements, making it an ideal solution for many applications.
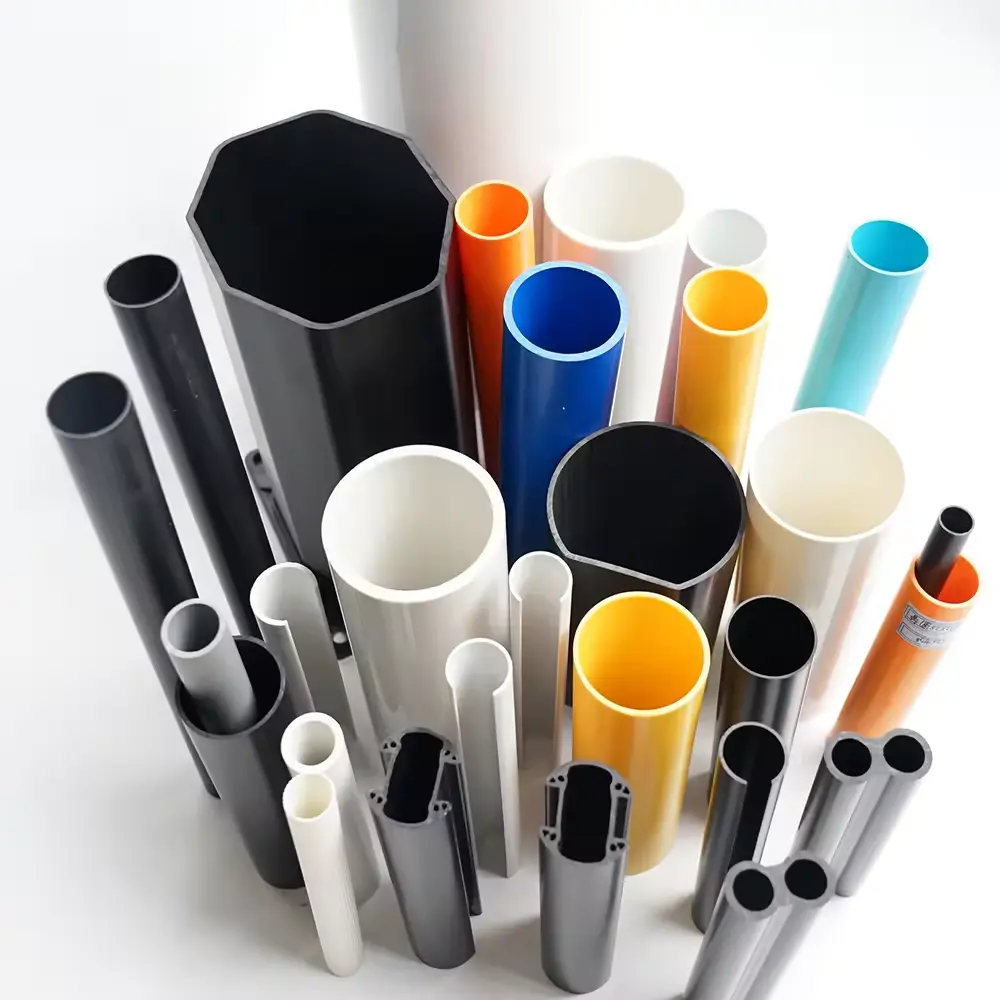
What is Custom Plastic Rod and Tube Extrusion?
Custom plastic rod and tube extrusion involves heating plastic resin until it becomes pliable and then forcing it through a specialized die to create rods and tubes of varying diameters and lengths. This process allows for precise control over the dimensions and properties of the finished product, making it an invaluable method for many industries.
Advantages of Custom Plastic Rod and Tube Extrusion
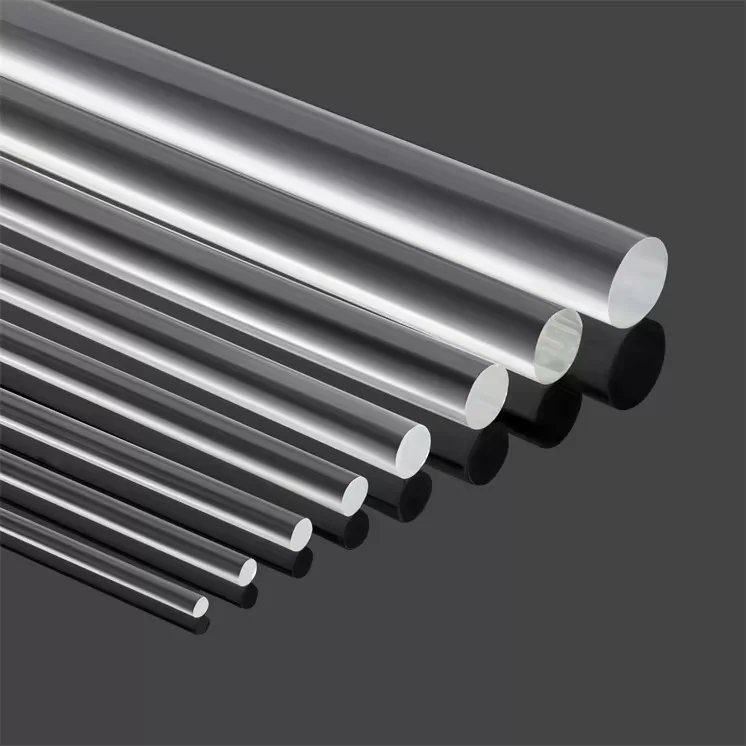
1. Tailored Designs
One of the primary advantages of custom plastic rod and tube extrusion is the ability to create tailored designs. Manufacturers can specify the exact dimensions, shapes, and properties required for their specific applications. This customization ensures that the final product meets precise requirements, leading to improved performance and functionality.
2. Material Versatility
Custom plastic extrusion can utilize various plastic materials, including polyvinyl chloride (PVC), polyethylene (PE), and nylon. This versatility allows manufacturers to select materials that offer the best properties for their applications, such as durability, flexibility, or chemical resistance.
3. Cost-Effectiveness
Custom plastic rod and tube extrusion is a cost-effective manufacturing method. By producing large quantities of extruded products, manufacturers can benefit from economies of scale, reducing production costs per unit. Additionally, the minimal waste generated during the extrusion process contributes to cost savings.
4. High Efficiency
The extrusion process is continuous, allowing for high production rates. This efficiency enables manufacturers to meet large order demands while maintaining consistent quality. Custom plastic rod and tube extrusion also minimizes lead times, ensuring that products are delivered promptly.
5. Durability and Strength
Extruded plastic rods and tubes often exhibit enhanced durability and strength compared to other manufacturing methods. The process allows for the alignment of polymer chains, resulting in improved tensile strength and resistance to impact, making them suitable for demanding applications.
6. Recyclability
Many materials used in custom plastic rod and tube extrusion are recyclable, making this process an environmentally friendly choice. Manufacturers can create products that contribute to sustainability initiatives, reducing waste and promoting a circular economy.
7. Design Flexibility
The ability to create complex shapes and designs is a significant advantage of custom plastic extrusion. Manufacturers can incorporate features such as grooves, slots, and varying wall thicknesses, which are challenging to achieve with other manufacturing methods.
Applications of Custom Plastic Rod and Tube Extrusion
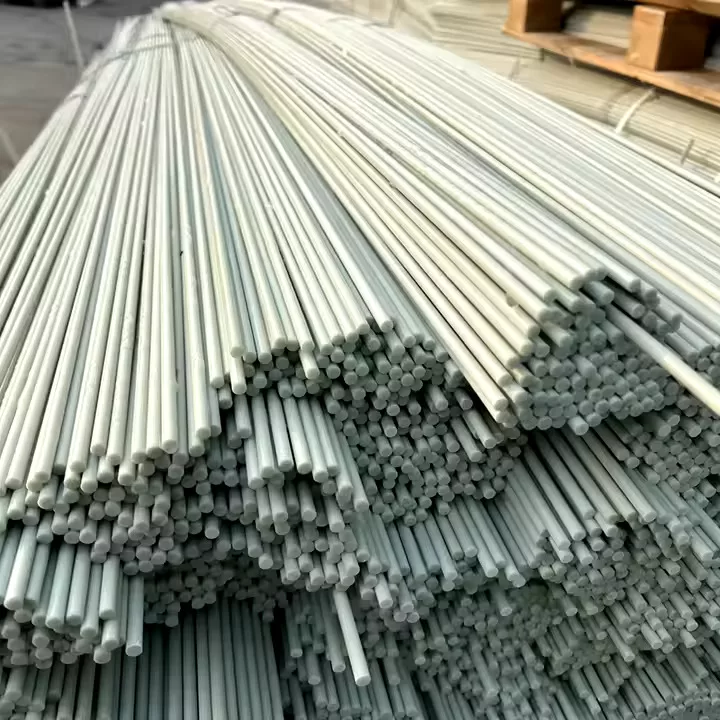
Custom plastic rod and tube extrusion is employed in various industries, including:
- Construction: Used for piping, window frames, and insulation materials.
- Automotive: Employed in components like weather stripping and trim.
- Electronics: Utilized for wiring insulation and protective housings.
- Medical: Commonly used in medical tubing and device housings.
- Packaging: Used for creating protective packaging and containers.
FAQs About Custom Plastic Rod and Tube Extrusion
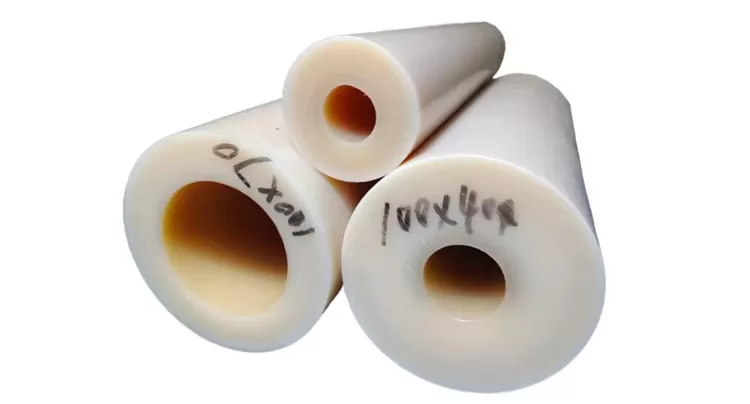
Q1: What materials can be used in custom plastic rod and tube extrusion?
A: Various materials can be used, including polyvinyl chloride (PVC), polyethylene (PE), nylon, and other thermoplastics, each offering unique properties suitable for different applications.
Q2: How does the extrusion process work?
A: In the extrusion process, plastic resin is heated until it becomes pliable, then forced through a specially designed die to create the desired shape. The extruded material is then cooled and cut to the required length.
Q3: Can custom plastic rod and tube extrusion create complex shapes?
A: Yes, custom plastic extrusion can create a wide range of shapes, including complex designs with features such as grooves, slots, and varying wall thicknesses.
Q4: Is custom plastic rod and tube extrusion cost-effective?
A: Yes, custom plastic extrusion is a cost-effective method, especially for large production runs, as it reduces waste and benefits from economies of scale.
Q5: Are extruded plastic products recyclable?
A: Many materials used in custom plastic rod and tube extrusion are recyclable, contributing to sustainability efforts and reducing environmental impact.
Conclusion
Custom plastic rod and tube extrusion offers a myriad of advantages, making it an essential manufacturing process across various industries. With tailored designs, material versatility, cost-effectiveness, and high efficiency, this technique provides solutions for a wide range of applications. As sustainability becomes increasingly important, the recyclability of extruded products further enhances its appeal.