ABS plastic profiles are widely used in the automotive industry due to their versatility, durability, and cost-effectiveness. ABS (Acrylonitrile Butadiene Styrene) is an engineering plastic that comes in different grades to suit various applications. These profiles are categorized based on impact strength, molding methods, and specific performance characteristics. In this article, we will explore the different grades of ABS plastic profiles and their applications in automobiles.
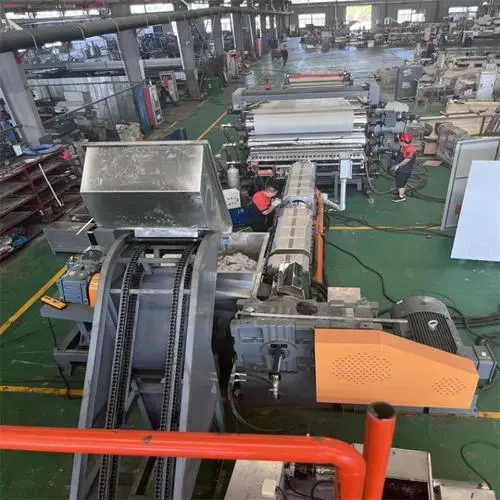
Types of ABS Plastic Profiles Used in Automobiles
ABS plastic profiles can be divided into several types, such as ultra-high impact, high impact, and medium impact, based on their impact strength. Additionally, they are classified by molding methods like injection, extrusion, and blow molding. According to specific use cases and performance characteristics, ABS profiles can further be subdivided into general, heat-resistant, electroplating, flame-retardant, transparent, extruded plate, and pipe profiles.
General Injection Grade ABS Plastic
The general injection grade ABS plastic profiles are the most widely used in the automotive industry. These are typically utilized for producing large, complex parts with high precision. For instance, a car dashboard made from ABS plastic is much more cost-efficient than one made from steel, which requires multiple processes like shearing, stamping, and painting. ABS plastic simplifies the manufacturing process to one injection or blow molding step.
Low-Odor ABS Plastic Profiles for Automotive Interiors
As automobile interiors increasingly focus on improving air quality, low-odor ABS plastic profiles have become essential. VOCs (volatile organic compounds) present in plastics can migrate to the surface and evaporate into the air inside the vehicle, posing potential health risks. By selecting the appropriate materials and processing methods, low-odor ABS profiles are designed to minimize these emissions.
Low-odor ABS materials are commonly used for:
- Door panels
- Instrument panel trims
- Glove boxes
- Central control panels
- Air-conditioning vents
These components, especially those exposed to higher temperatures, benefit from ABS profiles that ensure air quality and material stability.
Heat-Resistant ABS Plastic Profiles for High-Temperature Components
For parts exposed to higher temperatures, like air-conditioning vents and radiator grilles, heat-resistant ABS plastic profiles are crucial. A common method of enhancing heat resistance in ABS is by blending it with PC (polycarbonate) to create ABS/PC alloys. These alloys improve performance in heat-sensitive environments and help prevent deformation, which can affect the aesthetic and structural integrity of parts.
Heat-resistant ABS profiles are also used in:
- Door panels requiring impact resistance
- Fenders of high-end cars
The combination of impact resistance and heat resistance makes these profiles ideal for high-performance automotive applications.
Matting ABS Plastic Profiles for Interior Applications
Interior automotive components often require reduced gloss to avoid glare and discomfort for drivers. Matting ABS plastic profiles are specifically designed to reduce light reflection inside the car. ABS, naturally a high-gloss material, is modified during production to achieve a matte finish by incorporating resins with low gloss and fillers that increase surface roughness.
Matting ABS profiles are used in:
- Dashboards
- Steering wheel covers
- Door trims
These components help create a more comfortable driving experience by reducing glare and light reflection.
Electroplating Grade ABS Plastic Profiles for Aesthetic Components
While ABS is known for its excellent aesthetic qualities, electroplating grade ABS plastic profiles are often used when a superior finish is required. This grade is modified with rubber to enhance the polarity of the material, making it ideal for electroplating and other surface treatments.
Common applications of electroplating grade ABS profiles include:
- Radiator grilles
- Decorative logos
- Exterior trims
These parts benefit from the electroplating process to achieve a shiny, metallic finish that enhances the vehicle’s appearance.
Weather-Resistant ABS Plastic Profiles for Exterior Components
Weather-resistant ABS plastic profiles are essential for exterior automotive parts, as they are exposed to sunlight, heat, and other environmental factors. Standard ABS can degrade under prolonged exposure to UV radiation, leading to discoloration, loss of mechanical properties, and surface degradation. Weather-resistant ABS profiles are formulated to withstand these conditions, ensuring durability and longevity.
These profiles are often used for:
- Exterior trims
- Radiator grilles
- Mirror housings
ABS Plastic Profiles for Body Panels
One of the major challenges in automotive manufacturing is the plasticization of body panels, which include front and rear fenders, partitions, and panels. These components require materials with high impact resistance, heat resistance, and rigidity. ABS plastic profiles and ABS/PC alloys are increasingly used for this purpose, offering the strength and durability needed for exterior body parts while reducing the weight compared to traditional materials like steel.
Conclusion
In conclusion, ABS plastic profiles play a critical role in automotive manufacturing, providing solutions for both interior and exterior components. With different grades such as low-odor, heat-resistant, matting, and electroplating profiles, ABS is a versatile material that meets various performance requirements in vehicles. From improving air quality inside the car to ensuring the durability of exterior trims, ABS plastic profiles are an indispensable part of modern automotive design.