Plastic profile extrusion is a manufacturing process that transforms raw plastic materials into continuous shapes. This versatile technique is widely used in various industries, particularly in the production of consumer goods.
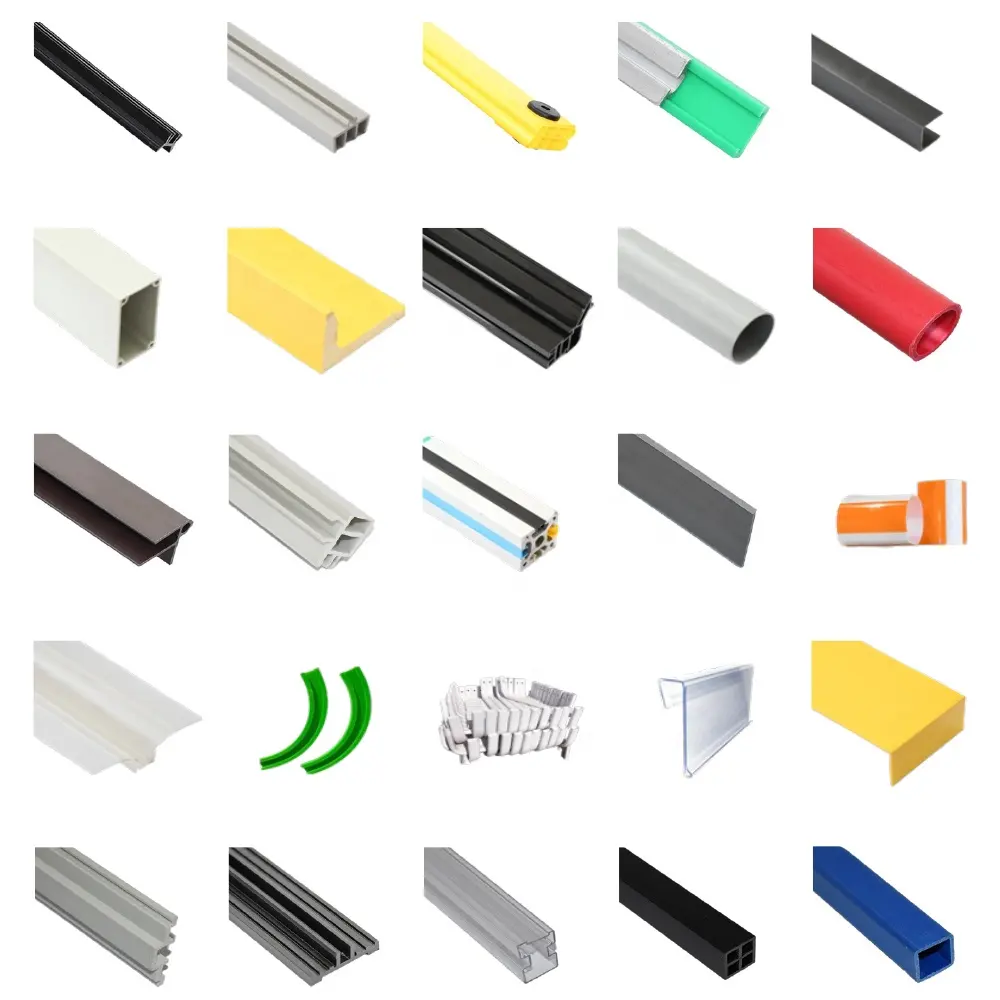
What is Plastic Profile Extrusion for Consumer Goods?
Plastic profile extrusion involves melting plastic pellets and forcing them through a die to create specific shapes. These extruded profiles can be solid, hollow, or complex in design, making them ideal for a wide range of applications in consumer goods. Common materials used in this process include PVC, polyethylene, and polypropylene.
Benefits of Custom Plastic Extrusion
- Versatility: Custom plastic extrusion allows for the production of various shapes and sizes, tailored to meet specific product requirements.
- Cost-Effective: When producing large quantities, plastic profile extrusion can significantly reduce manufacturing costs compared to other methods.
- Consistency and Quality: This process ensures uniformity in product dimensions, enhancing quality control and reducing waste.
- Customization: Businesses can design unique profiles to differentiate their products in the market, from color variations to specialized shapes.
Applications of Plastic Profile Extrusion in Consumer Goods
1. Packaging Solutions
Custom plastic extrusion is heavily utilized in the packaging industry, providing solutions such as flexible film, rigid containers, and custom-shaped packaging for various consumer goods.
2. Home and Garden Products
From window frames to garden edging, plastic extrusions offer durability and weather resistance, making them ideal for outdoor products.
3. Automotive Components
Many automotive parts, such as seals and trims, are produced using plastic profile extrusion, ensuring lightweight and durable solutions.
4. Electrical and Electronics
Cable management systems, conduits, and insulation materials are often made through this process, providing safety and functionality in consumer electronics.
The Custom Plastic Extrusion Process
Step 1: Material Selection
Choosing the right plastic material is crucial for the desired characteristics of the final product. Factors such as flexibility, strength, and resistance to environmental factors should be considered.
Step 2: Design and Prototyping
Collaboration between designers and manufacturers is essential. Creating a prototype helps visualize the final product and allows for adjustments before full-scale production.
Step 3: Extrusion
Once the design is finalized, the material is heated and extruded through a die to form the desired profile. This step is critical in ensuring precision and quality.
Step 4: Cooling and Finishing
After extrusion, the profiles are cooled and cut to the specified lengths. Additional processes, such as trimming or surface finishing, may also be performed to enhance the final product.
Key Considerations for Choosing a Plastic Extrusion Partner
1. Experience and Expertise
Select a plastic extrusion manufacturer with a proven track record in custom plastic extrusion. Experience in your specific industry can ensure better outcomes.
2. Technology and Equipment
Advanced machinery and technology play a significant role in the quality and efficiency of the extrusion process. Ensure the partner uses state-of-the-art equipment.
3. Quality Control
A reputable partner will have stringent quality control measures in place to maintain consistency and product integrity.
4. Customer Support
Effective communication and support throughout the process are vital. Choose a partner that values collaboration and responsiveness.
Conclusion
Custom plastic extrusion for consumer goods offers immense potential for businesses looking to innovate and improve their product offerings. By understanding the process, applications, and key considerations, companies can leverage plastic profile extrusion to create high-quality, customized products that meet market demands. Embrace the advantages of this manufacturing method and transform your product designs into reality.
Call to Action
Are you ready to explore custom plastic extrusion for your consumer goods? Contact us today to learn more about how we can help you bring your unique ideas to life!