Manufacturing plastic extrusion profile molds is a complex process, primarily due to the intricate designs involved and the high standards of precision required. This article delves into the challenges faced in creating these molds and the factors that contribute to their complexity.
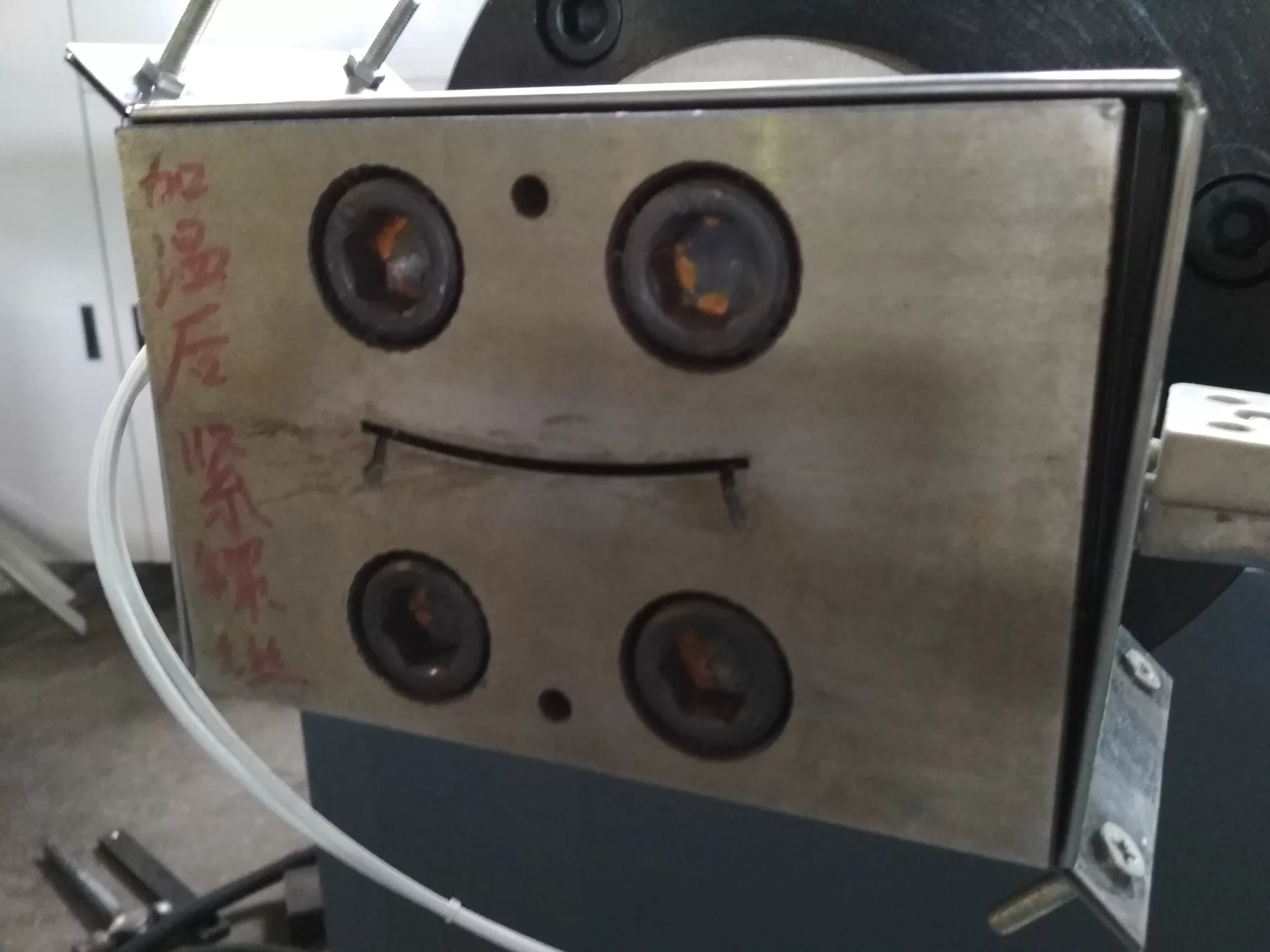
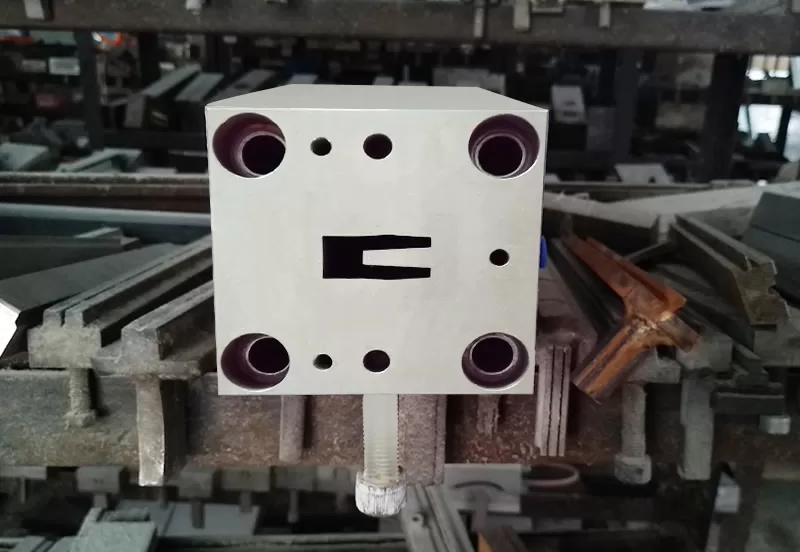
Understanding the Complexity of Plastic Extrusion Profile Molds
Plastic extrusion profile molds consist of two main components: the cavity and the core. These elements create the mold’s external and internal shapes, which are three-dimensional surfaces. The complexity of these surfaces makes them difficult to process, particularly the inner molding surfaces of blind holes within the cavity. Traditional processing methods often require skilled technicians, numerous auxiliary fixtures, and extended processing times, resulting in a lengthy and challenging production cycle.
Stringent Precision and Quality Standards
The manufacturing of plastic extrusion profile molds is governed by strict dimensional accuracy and surface quality requirements. Currently, general plastic parts require dimensional accuracy within the IT6-7 range and surface roughness of RA0.2-0.1 μm. In comparison, injection mold parts demand even tighter tolerances, typically IT5-6, with surface roughness of RA0.1 μm or lower.
For specialized applications, such as laser disk recording surfaces, the mold roughness must reach an impressive level of 0.01 μm or less. This necessitates high-quality, long-lasting injection molds that can withstand over 1 million cycles, improving efficiency and reducing costs.
Structural Considerations for Precision Injection Molds
To achieve the necessary precision, plastic extrusion profile molds must employ robust structural designs. High rigidity mold frames, thicker templates, and additional support columns or conical positioning elements are essential to prevent deformation under internal pressures, which can sometimes exceed 100 MPa.
Moreover, the design of the ejector device plays a crucial role in maintaining dimensional accuracy and preventing product deformation. Selecting optimal ejection points ensures uniform demolding across all locations, which is vital for maintaining the quality of the final product.
Challenges of Long Processing Times and Tight Deadlines
The manufacturing process for plastic extrusion profile molds can be time-consuming, especially when dealing with specially-shaped materials that need to fit precisely with other components. Often, while other parts are ready, the corresponding injection molded parts are still undergoing development, which can lead to tight delivery timelines.
Given the high dimensional accuracy and varying characteristics of resin materials, molds often require repeated testing and adjustments post-manufacturing. This iterative process further compresses development timelines, adding to the overall complexity.
The Importance of Integrated Design and Manufacturing
One of the significant challenges in manufacturing plastic extrusion profile molds arises from the separation between design and production locations. While mold manufacturers create molds based on user specifications, the actual production of profile products often occurs at different facilities. This fragmentation can lead to discrepancies between product design, mold design, and production quality.
To ensure that the extruded profiles meet high-quality standards, it is crucial that the design and manufacturing processes occur within a single facility. This integration fosters better communication and quality control throughout the production process, ultimately enhancing the reliability and performance of plastic extrusion profile molds.
Conclusion
Manufacturing plastic extrusion profile molds is fraught with challenges, from the complexity of three-dimensional surfaces to stringent precision and quality requirements. Addressing these challenges requires skilled technicians, advanced technology, and a cohesive approach to design and production. By understanding the intricacies of this process, manufacturers can better navigate the obstacles and enhance the quality of their plastic extrusion profile molds.