Two-color or multi-material plastic co-extrusion involves combining different materials or colors in a single extrusion process. This technique offers versatile possibilities for creating unique and functional products.
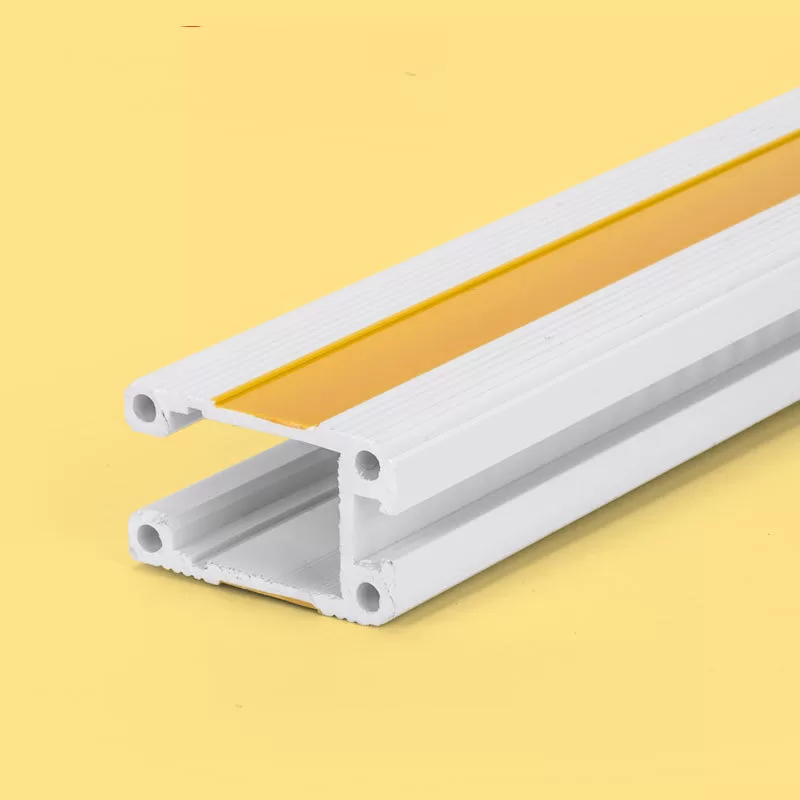
Multi-Color Plastic Co-Extrusion
Multi-color co-extrusion involves using different colored plastic materials without allowing them to intermix. This technique is commonly used to create products with distinct color patterns or logos, such as buttons or car lights.
Multi-Material Plastic Co-Extrusion
Multi-material co-extrusion combines different types of plastic materials, often offering enhanced properties. Common combinations include:
- Rigid and Hard: Combining thermoplastic materials with thermoplastic elastomers (TPE, TPU) creates products with a rigid, corrosion-resistant outer layer and a soft, shock-resistant inner core.
- Liquid Silicone Rubber (LSR): LSR’s temperature resistance and mechanical properties make it a valuable addition to multi-material extrusions. However, it requires careful mold design to prevent thermal insulation issues.
- Electroplating/Conductive Materials: Combining these materials with non-conductive materials enables the production of three-way conductive parts.
- In-Mold Assembly: This technique combines incompatible materials to create interconnected or movable parts within a single extrusion.
Key Considerations of Plastic Co-Extrusion
When combining different materials, factors like adhesion, shrinkage rates, thermal expansion coefficients, and molding temperatures must be carefully considered. Mechanical connections or chemical reactions can enhance bonding strength where necessary.
Conclusion
Two-color and multi-material co-extrusion provide a wide range of possibilities for creating unique and functional plastic products. By understanding the various material combinations and their specific requirements, you can effectively select the right plastic extrusion manufacturer to design and produce products that meet your desired specifications.