PC lampshade strips are common in everyday lighting, available in various colors like blue, red, white, and transparent, with different material types and translucencies. But how exactly are these PC lampshade strips made? The answer lies in the extrusion molding process, a crucial manufacturing method for shaping these versatile lampshades.
Understanding the Extrusion Molding Process for PC Lampshade Strips
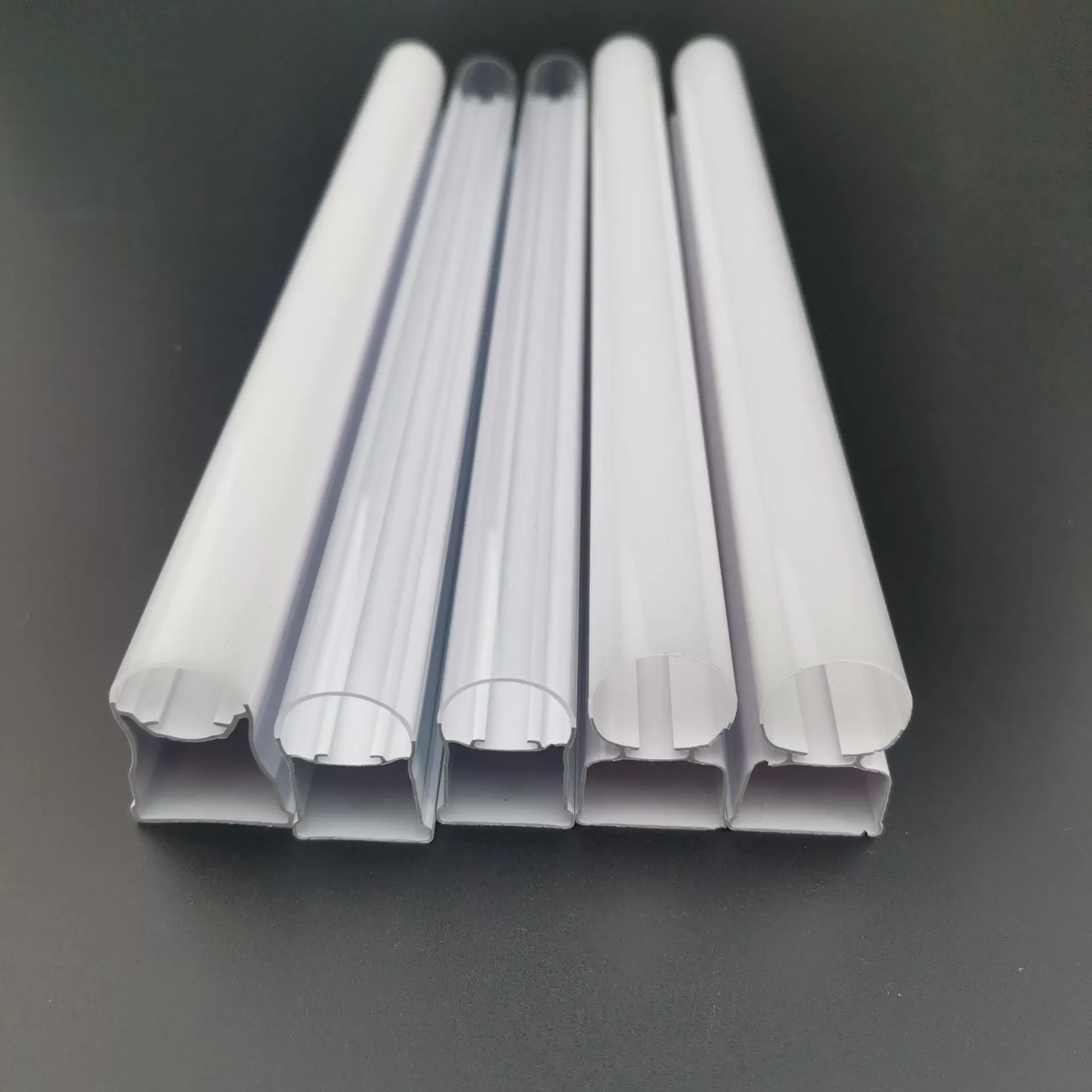
Extrusion molding is a continuous process used to produce PC (polycarbonate) lampshades by pushing melted plastic material through a die, which shapes it into the desired form. The process ensures uniformity and efficiency in producing high-quality lampshades used in the lighting industry.
PC Lampshade Strip Extrusion Equipment
Before diving into the extrusion molding principle, it’s essential to understand the types of equipment involved in producing PC lampshade strips. Plastic extruders play a central role, and they come in different types:
- Twin-Screw Extruders
- Single-Screw Extruders
- Multi-Screw Extruders (Rare)
- Screwless Extruders (Rare)
Each of these machines has specific applications, but twin-screw and single-screw extruders are the most commonly used in PC lampshade strip production.
How Does a PC Lampshade Strip Extruder Work?
The working principle of the screw extruder is based on the pressure and shear force generated by the rotating screw. This force allows the raw PC material to melt, mix, and plasticize as it moves through the barrel. Once the material is uniformly plasticized, it passes through a die that shapes the material into the desired lampshade strip form.
Key Steps in the Extrusion Process:
- Plasticization
The raw polycarbonate is heated and melted as it moves through the screw mechanism. This phase ensures that the material is in the correct state for shaping. - Mixing
The rotating screw ensures the material is thoroughly mixed, preventing any uneven distribution or imperfections in the final product. - Shaping through the Die
Once the material is fully melted and mixed, it passes through a die. The die is designed according to the specific dimensions and shape of the PC lampshade strip. - Cooling and Cutting
After exiting the die, the newly formed PC lampshade strip is cooled and cut to the desired length, ready for final use.
The Role of Plunger Extruders
Another type of extrusion equipment used in some cases is the plunger extruder. Unlike screw extruders, the plunger extruder uses pressure to push pre-plasticized material through a die. However, this method is less common in producing PC lampshade strips because it results in discontinuous production and lacks thorough mixing of the material.
Plunger extruders are typically used for materials with poor fluidity or very high viscosity, such as nitrocellulose plastics. However, due to the continuous production and superior mixing abilities of screw extruders, they are preferred for PC lampshade strip manufacturing.
Advantages of PC Lampshade Strips in Lighting
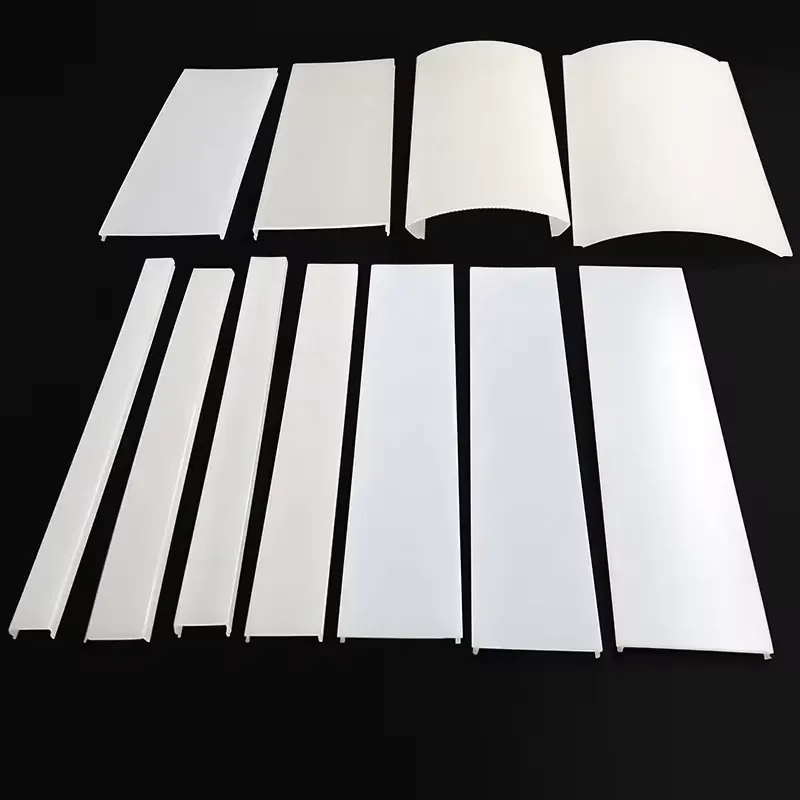
The primary function of PC lampshade strips is to diffuse light effectively, making it softer and more focused while minimizing glare from LED light sources.
Here are some benefits of using PC lampshade strips:
- Light Diffusion
PC lampshades help gather and distribute light more evenly, providing a softer, more pleasant lighting experience without harsh glares. - High Durability
PC material has a higher specific strength than some metals, such as alloy aluminum. This makes it an ideal choice for long-lasting lighting solutions. - Excellent Insulation Properties
PC lampshades offer superior insulation, both electrically and thermally, making them safe to use in various lighting applications. - Shockproof and Heat Resistant
PC lampshades have excellent shockproof and heat-resistant qualities, allowing them to withstand demanding environments, including industrial and outdoor settings. - Versatility of Material
PC lampshades can be made from various materials, but polycarbonate is favored due to its outstanding combination of strength, light diffusion, and insulation properties.
Conclusion
The extrusion molding process for PC lampshade strips is a highly efficient and effective method for producing durable, high-performance lighting components. The use of screw extruders ensures continuous production with thorough plasticization and mixing, while the versatility of polycarbonate material provides excellent light diffusion, strength, and insulation.
For any lighting design that requires reliability and quality, PC lampshade strips are a superior choice, combining functionality with aesthetic appeal.