Plastic co-extrusion is a popular and efficient manufacturing process in which two or more layers of different plastic materials are extruded simultaneously to form a single product. It’s widely used across various industries, from packaging to automotive, due to its versatility and ability to combine the properties of multiple materials in a single piece.
What is Plastic Co-Extrusion?
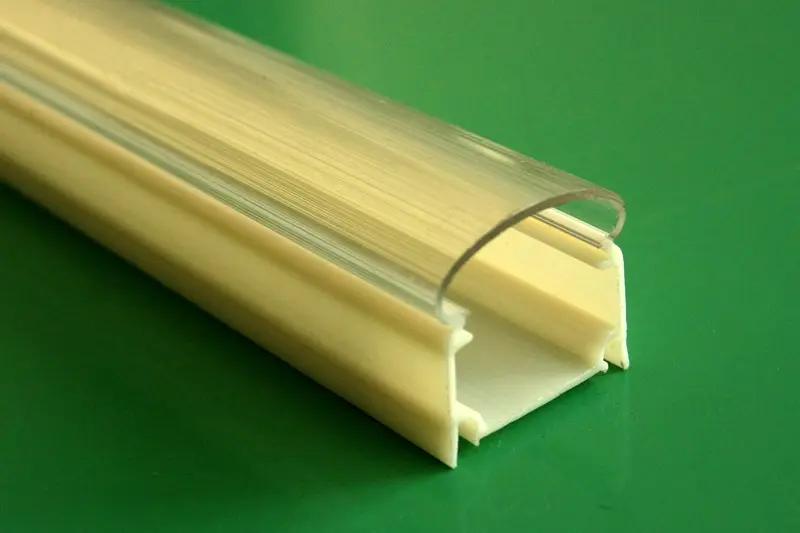
Plastic co-extrusion is the process of extruding two or more thermoplastic materials through a single die to create a multi-layered product. This technology allows manufacturers to combine materials with different properties, such as flexibility, strength, and chemical resistance, in a single output.
During co-extrusion, each plastic layer is melted separately and combined while in a molten state. The result is a composite structure that retains the distinct characteristics of each material, improving overall product performance.
Key Components of the Co-Extrusion Process
- Extruders: Each material is fed into its own extruder, where it’s heated until it melts.
- Feed Block: The molten materials are then directed into a feed block, where they are combined into layers.
- Die: The combined material is pushed through a die, forming the desired shape or profile.
- Cooling and Sizing: The extruded product is cooled and sized to the desired specifications before being cut or rolled for storage.
Benefits of Plastic Co-Extrusion
1. Cost-Effective Material Usage
By using co-extrusion, manufacturers can utilize expensive materials only in the outer layers of the product, while the inner layers are made from less costly materials. This method reduces material costs without compromising product quality.
2. Enhanced Product Properties
Co-extrusion allows for the combination of different plastics to improve the overall properties of the finished product. For example, one layer could provide rigidity, while another adds flexibility, offering enhanced durability and performance.
3. Customization and Flexibility
Plastic co-extrusion offers a high degree of customization. Different materials, colors, textures, and thicknesses can be combined in a single product, making it ideal for a wide range of applications, from packaging to industrial components.
4. Improved Barrier Properties
In packaging applications, co-extrusion enables the creation of materials with excellent barrier properties. One layer may offer protection against moisture, while another layer might prevent the permeation of gases, ensuring longer shelf life for products.
Common Applications of Plastic Co-Extrusion
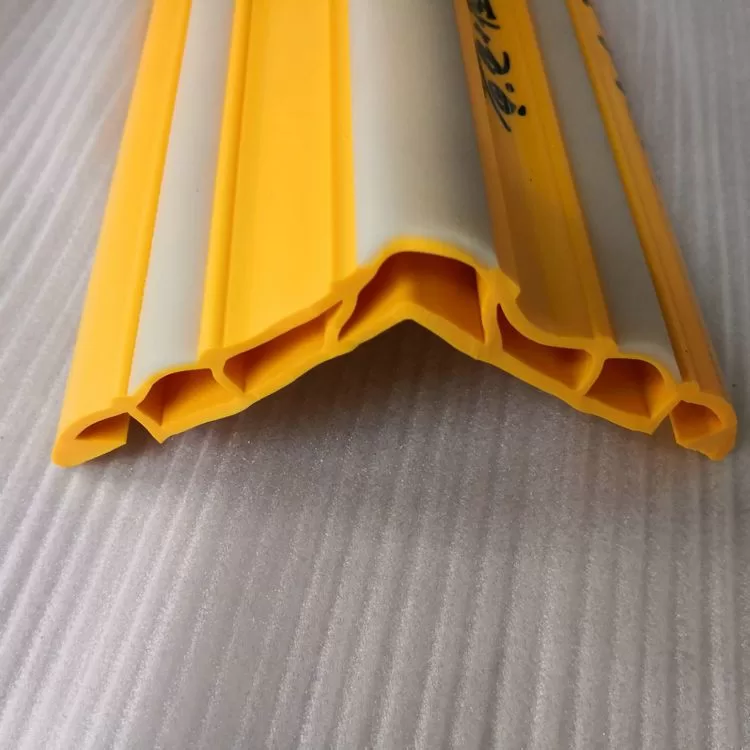
1. Packaging
Plastic co-extrusion is widely used in the packaging industry to create multi-layer films and containers. These products often require specific properties, such as moisture resistance, flexibility, or durability, all of which can be achieved by combining different materials through co-extrusion.
2. Building and Construction
In construction, plastic co-extrusion is used to produce items like pipes, window profiles, and weather seals. The process allows manufacturers to create products with a tough, UV-resistant outer layer and a durable, cost-effective inner core.
3. Automotive Components
The automotive industry also benefits from plastic co-extrusion for creating parts that need to withstand high stress while maintaining flexibility and resistance to environmental factors. Examples include weather stripping, seals, and certain interior components.
4. Medical Equipment
In the medical industry, co-extruded plastic tubing is commonly used for delivering fluids or gases. These tubes often require several layers, each contributing to the overall function of the device, such as flexibility, transparency, and resistance to chemicals.
Types of Plastic Used in Co-Extrusion
Several different types of plastics can be used in co-extrusion, depending on the desired properties of the final product. Some common materials include:
- Polyethylene (PE): Known for its flexibility and durability, polyethylene is often used in packaging and tubing.
- Polyvinyl Chloride (PVC): PVC is widely used for its rigidity and weather resistance, making it ideal for construction products.
- Polypropylene (PP): Offering high resistance to chemicals and moisture, polypropylene is used in various automotive and packaging applications.
- Ethylene Vinyl Acetate (EVA): EVA is soft, flexible, and often used in applications requiring elasticity and toughness.
How to Choose the Right Co-Extrusion Process for Your Needs
When considering plastic co-extrusion for your manufacturing needs, there are a few factors to keep in mind:
- Material Compatibility: Ensure that the materials you plan to use are compatible and will bond well during the co-extrusion process.
- Application Requirements: Identify the key performance characteristics your product needs, such as strength, flexibility, or chemical resistance, and select materials that offer these properties.
- Production Volume: The complexity of co-extrusion may increase setup costs, so it’s important to evaluate the expected production volume to ensure cost efficiency.
Conclusion
Plastic co-extrusion is an advanced manufacturing process that allows for the creation of products with enhanced properties and reduced costs. Its ability to combine multiple materials into a single product opens up endless possibilities for customization across industries. By understanding the basics of co-extrusion, its benefits, and its applications, manufacturers can make informed decisions on how to best utilize this technology in their production processes.