Plastic extrusion is a crucial process in modern manufacturing, known for producing continuous, uniform plastic products. A key factor in its success is the design and tooling involved in shaping raw plastic into finished products. In this guide, we’ll explore the principles of plastic extrusion design and tooling, offering insights into how manufacturers create efficient, high-quality extrusion processes.
1. What is Plastic Extrusion Design?
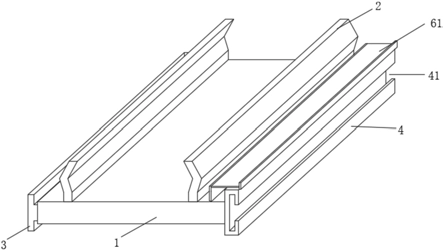
Plastic extrusion design refers to the planning and engineering of the shape, size, and structure of the plastic product to be manufactured through extrusion. This process involves creating a design that can be accurately produced using the extrusion die and other tooling components. The design determines the product’s cross-sectional profile, ensuring it meets the required specifications for its intended application.
Extrusion design is essential because it directly impacts the quality, functionality, and manufacturability of the plastic product. Whether you’re designing simple tubes, complex profiles, or multi-layered structures, getting the design right is critical for a successful extrusion process.
2. Understanding Plastic Extrusion Tooling
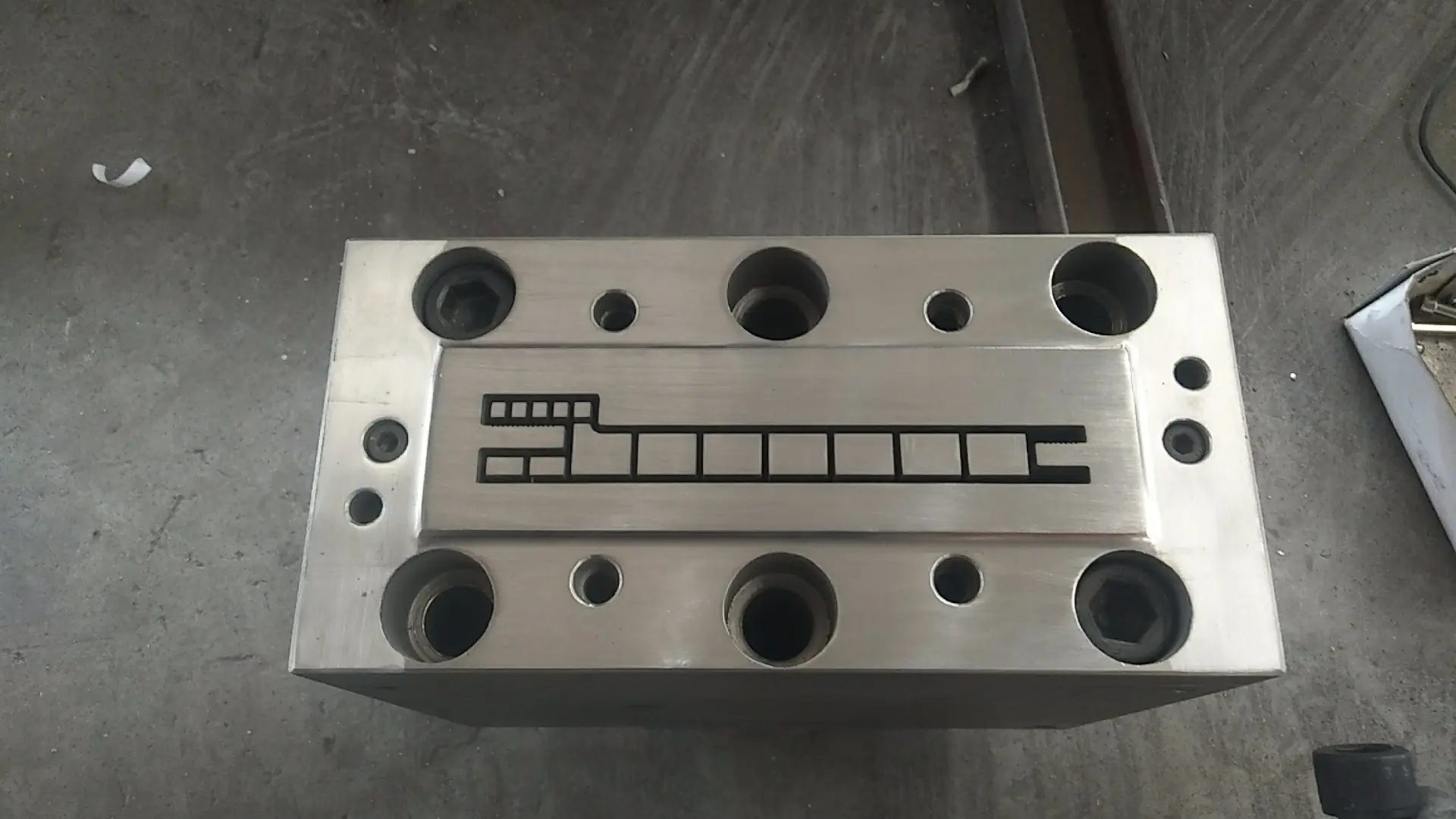
Plastic extrusion tooling refers to the tools and equipment used to shape molten plastic as it moves through the extruder. The most important component of this tooling is the extrusion die, which dictates the final shape of the product. Tooling also includes other critical components like calibrators, cooling tanks, and cutters that ensure the product maintains its shape and size after exiting the die.
The precision of the extrusion tooling determines the dimensional accuracy, surface finish, and overall quality of the extruded plastic products. Proper tooling design allows for seamless and efficient production, reducing material waste and ensuring consistency.
3. Key Considerations in Plastic Extrusion Design
Designing for plastic extrusion requires careful consideration of several factors that affect both the product’s performance and the efficiency of the manufacturing process. Here are some key elements:
A. Wall Thickness
Maintaining a uniform wall thickness throughout the product is essential to avoid warping or defects. Variations in wall thickness can lead to inconsistent cooling rates, which affect the product’s strength and appearance.
B. Material Selection
The type of plastic used (e.g., PVC, PE, PP, ABS) plays a significant role in the design process. Different plastic materials have varying melt flow rates, which influence the product’s behavior during extrusion and cooling.
C. Tolerances
Extrusion design must include tight tolerances to ensure dimensional accuracy. This is especially important for products like tubing, seals, or profiles that need to fit precisely with other components.
D. Cooling and Shrinkage
Extruded products undergo shrinkage as they cool. Designers must account for this by adjusting the dimensions in the design phase to ensure that the final product meets specifications after cooling.
4. Types of Extrusion Dies and Tooling
There are several types of extrusion dies and tooling setups that manufacturers use, each suited to specific applications:
A. Flat Die
Flat dies are used to produce plastic sheets and films. The molten plastic is spread across a wide surface, and the thickness of the sheet is controlled by adjusting the die gap.
B. Round Die
Round dies are ideal for creating tubular or cylindrical products like pipes and hoses. These dies have circular openings that shape the plastic into the desired cross-section.
C. Profile Die
Profile dies are custom-made to create specific, often complex cross-sectional shapes. These dies are used in applications like window frames, seals, or custom plastic profiles.
D. Co-extrusion Die
In co-extrusion, multiple layers of different materials are extruded simultaneously through a specialized die. This allows manufacturers to combine properties like strength, flexibility, or barrier performance into a single product.
5. The Role of Computer-Aided Design (CAD) in Extrusion
Computer-Aided Design (CAD) plays a vital role in modern plastic extrusion design. CAD software allows engineers to create detailed models of the extrusion die and the final product, helping to visualize and test designs before manufacturing begins. Using CAD, designers can:
- Optimize cross-sectional profiles for material flow and strength.
- Simulate extrusion processes to detect potential issues like flow imbalance or pressure drops.
- Reduce prototyping time, leading to faster production cycles.
By integrating CAD into the extrusion design process, manufacturers can achieve greater precision, reduce errors, and improve overall efficiency.
6. Common Materials Used in Plastic Extrusion Tooling
The materials used in the construction of extrusion dies and tooling must withstand the high temperatures and pressures of the extrusion process. Common materials include:
- Tool Steel: Known for its strength and heat resistance, tool steel is a popular choice for die construction.
- Stainless Steel: Corrosion-resistant and durable, stainless steel is often used in food or medical-grade extrusion processes.
- Carbide: For applications that require extreme precision, carbide dies offer high wear resistance and longevity.
These materials help maintain die accuracy, reduce wear, and prolong the lifespan of the tooling, contributing to cost-effective production.
7. Challenges in Plastic Extrusion Design and Tooling
Several challenges may arise during plastic extrusion design and tooling, including:
- Flow Imbalances: Inconsistent material flow through the die can lead to uneven product surfaces or thickness variations. Proper die design and testing are critical to address this.
- Die Wear: Continuous use of extrusion dies can lead to wear, which affects the precision of the final product. Regular maintenance and material selection can minimize this issue.
- Heat Management: Controlling the heat during extrusion is crucial to ensure the material flows smoothly through the die. Poor heat management can cause issues like melt fracture or surface imperfections.
8. Future Trends in Plastic Extrusion Design and Tooling
As the manufacturing industry evolves, so does plastic extrusion design and tooling. Here are some future trends to watch for:
A. 3D Printing for Prototyping
3D printing technology is increasingly being used to create prototypes of extrusion dies, allowing manufacturers to test designs quickly and at a lower cost.
B. Advanced Simulation Tools
Simulation software is becoming more advanced, allowing engineers to simulate material flow, cooling rates, and even shrinkage behavior before physical tooling is created.
C. Sustainable Design
Sustainability is driving innovation in plastic extrusion design. New materials and die designs are being developed to reduce waste, recycle more plastics, and increase energy efficiency.
Conclusion
Plastic extrusion design and tooling are essential components of the manufacturing process, determining the quality and efficiency of the final product. By carefully considering factors like material selection, die design, and modern CAD tools, manufacturers can create high-performance products while reducing costs and improving sustainability. As technology continues to evolve, innovations in design and tooling will drive further advancements in the plastic extrusion industry.