Plastic profile extrusion is a vital manufacturing process that shapes plastic materials into continuous profiles for a variety of applications. This versatile technique is increasingly used across various industries due to its efficiency, cost-effectiveness, and the ability to create complex shapes.
What is Plastic Profile Extrusion?
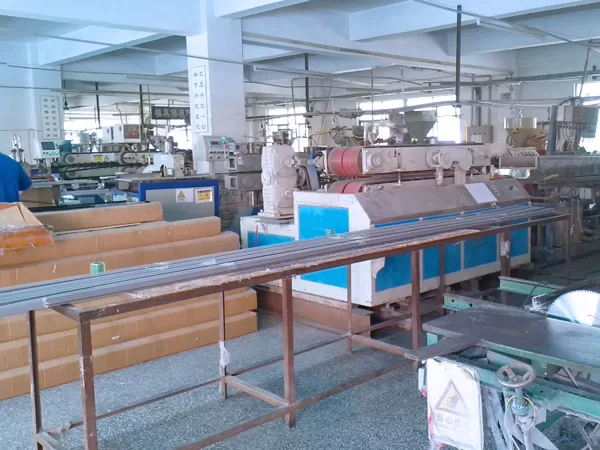
Plastic profile extrusion involves melting plastic pellets and forcing them through a die to create a continuous profile with a specific cross-sectional shape. This process is widely used to produce materials in different lengths, allowing manufacturers to create products tailored to specific needs. The most common materials used in this process include PVC, ABS, polycarbonate, and polyethylene.
1. Building and Construction
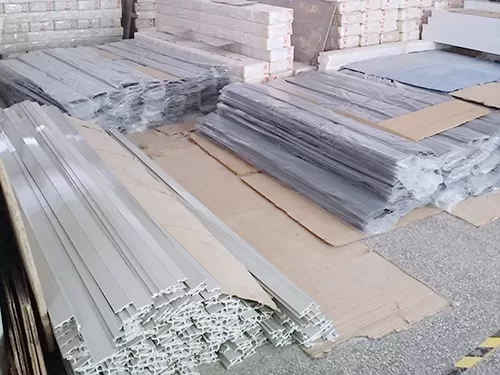
One of the most prominent applications of plastic profile extrusion is in the building and construction industry. Extruded plastic profiles are used for:
- Window Frames: PVC window frames are lightweight, durable, and offer excellent thermal insulation.
- Doors and Fencing: Custom extruded profiles for doors and fencing provide weather resistance and low maintenance.
- Roofing and Siding: Plastic profiles for roofing and siding offer durability and aesthetic versatility.
Benefits for Building and Construction
Using plastic profile extrusion in construction leads to improved energy efficiency and reduced maintenance costs, making it an ideal choice for modern architectural projects.
2. Automotive Industry
In the automotive sector, plastic profile extrusion plays a crucial role in manufacturing various components. Key applications include:
- Trim and Molding: Custom extruded profiles are used for interior and exterior trim, providing both functionality and style.
- Seals and Gaskets: Plastic extrusions for seals and gaskets enhance vehicle insulation and reduce noise.
- Bumpers and Body Panels: Lightweight plastic profiles contribute to improved fuel efficiency without compromising safety.
Advantages in Automotive Manufacturing
The use of plastic profile extrusion in automotive manufacturing results in reduced weight, enhanced performance, and lower production costs.
3. Electrical and Electronics
Plastic profile extrusion is essential in the electrical and electronics industry. Its applications include:
- Cable Management: Extruded profiles are used for cable trays and conduits, facilitating efficient cable organization.
- Enclosures: Custom profiles protect sensitive electronic components from environmental factors.
- Connectors and Clips: Precision extruded profiles are integral to various connector designs, ensuring reliable performance.
Impact on Electrical and Electronics
The flexibility and durability of extruded plastic profiles enhance the reliability and efficiency of electrical and electronic systems.
4. Consumer Goods
In the consumer goods sector, plastic profile extrusion is utilized to manufacture a variety of products, such as:
- Household Items: From storage solutions to furniture components, extruded profiles are versatile and practical.
- Sporting Goods: Custom profiles for sporting equipment improve performance and safety.
- Packaging: Innovative packaging solutions benefit from lightweight and durable plastic profiles.
Contribution to Consumer Goods
The ability to produce customized shapes and sizes makes plastic profile extrusion a favored choice in the consumer goods market.
5. Medical Devices
The medical industry increasingly relies on plastic profile extrusion for manufacturing critical components. Applications include:
- Medical Tubing: Customized extruded profiles are essential for various medical tubing applications, ensuring safety and efficiency.
- Casings and Enclosures: Durable plastic profiles protect sensitive medical devices from contamination and damage.
- Supports and Braces: Lightweight extruded profiles are used in supports and braces for patient care.
Importance in Medical Manufacturing
The precision and reliability of extruded plastic profiles are crucial for maintaining high standards in medical device manufacturing.
Conclusion
Plastic profile extrusion is an indispensable process in modern manufacturing, offering a wide range of applications across multiple industries. From construction to automotive, electrical, consumer goods, and medical devices, the benefits of this technique—such as efficiency, customization, and durability—make it a key player in advancing manufacturing capabilities. As technology continues to evolve, the potential for plastic profile extrusion will only expand, reinforcing its position in the manufacturing landscape.
By understanding the various applications and benefits of plastic profile extrusion, plastic extrusion manufacturers can leverage this technology to enhance product offerings and meet the demands of a rapidly changing market.