Plastic profile extrusion is a vital process in the manufacturing industry, enabling the creation of a wide range of products used in various applications. This comprehensive guide will delve into the fundamentals of plastic profile extrusion, its benefits, applications, and best practices for optimization.
What is Plastic Profile Extrusion?
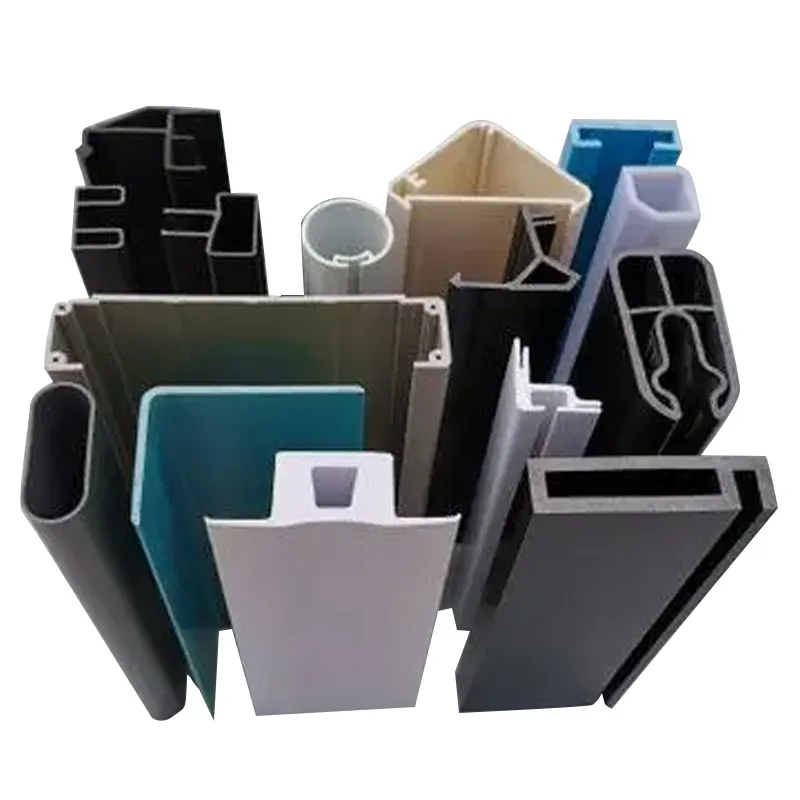
Plastic profile extrusion is a manufacturing process where plastic material is melted and shaped into continuous profiles through a die. The process involves several stages, including material selection, heating, shaping, and cooling, resulting in products such as window frames, tubing, and custom shapes.
The Extrusion Process Explained
- Material Selection
The first step in plastic profile extrusion is choosing the right type of plastic. Common materials include PVC, polyethylene, and polystyrene, each offering unique properties suitable for different applications. - Feeding
Raw plastic pellets are fed into a hopper and transported into the extruder, where they are heated to their melting point. - Melting
As the pellets move through the extruder, they are subjected to heat and pressure, causing them to melt into a viscous flow. - Shaping
The molten plastic is forced through a die that shapes it into the desired profile. This stage is critical as the design of the die directly influences the final product’s dimensions and characteristics. - Cooling
Once the plastic exits the die, it is cooled, solidifying into the desired shape. This can be achieved through water baths, air cooling, or other methods. - Cutting and Finishing
The final stage involves cutting the extruded profile to the required lengths and adding any necessary finishing touches, such as surface treatment or coating.
Benefits of Plastic Profile Extrusion
Plastic profile extrusion offers several advantages that make it a preferred manufacturing method:
- Cost-Effectiveness: Extrusion allows for high-volume production, reducing the per-unit cost of manufacturing.
- Versatility: The process can create a wide variety of shapes and sizes, accommodating diverse applications.
- Material Efficiency: Extrusion minimizes waste, as any excess material can often be recycled and reused.
- Customization: Manufacturers can easily modify designs to meet specific customer requirements, enabling tailored solutions.
Applications of Plastic Profile Extrusion
Plastic profile extrusion finds its application in numerous industries, including:
- Construction: Used for window frames, doors, and various structural components.
- Automotive: Producing parts like trim, seals, and dashboards.
- Electrical: Creating conduits and cable management systems.
- Consumer Goods: Manufacturing items such as household products and toys.
Best Practices for Optimizing Plastic Profile Extrusion
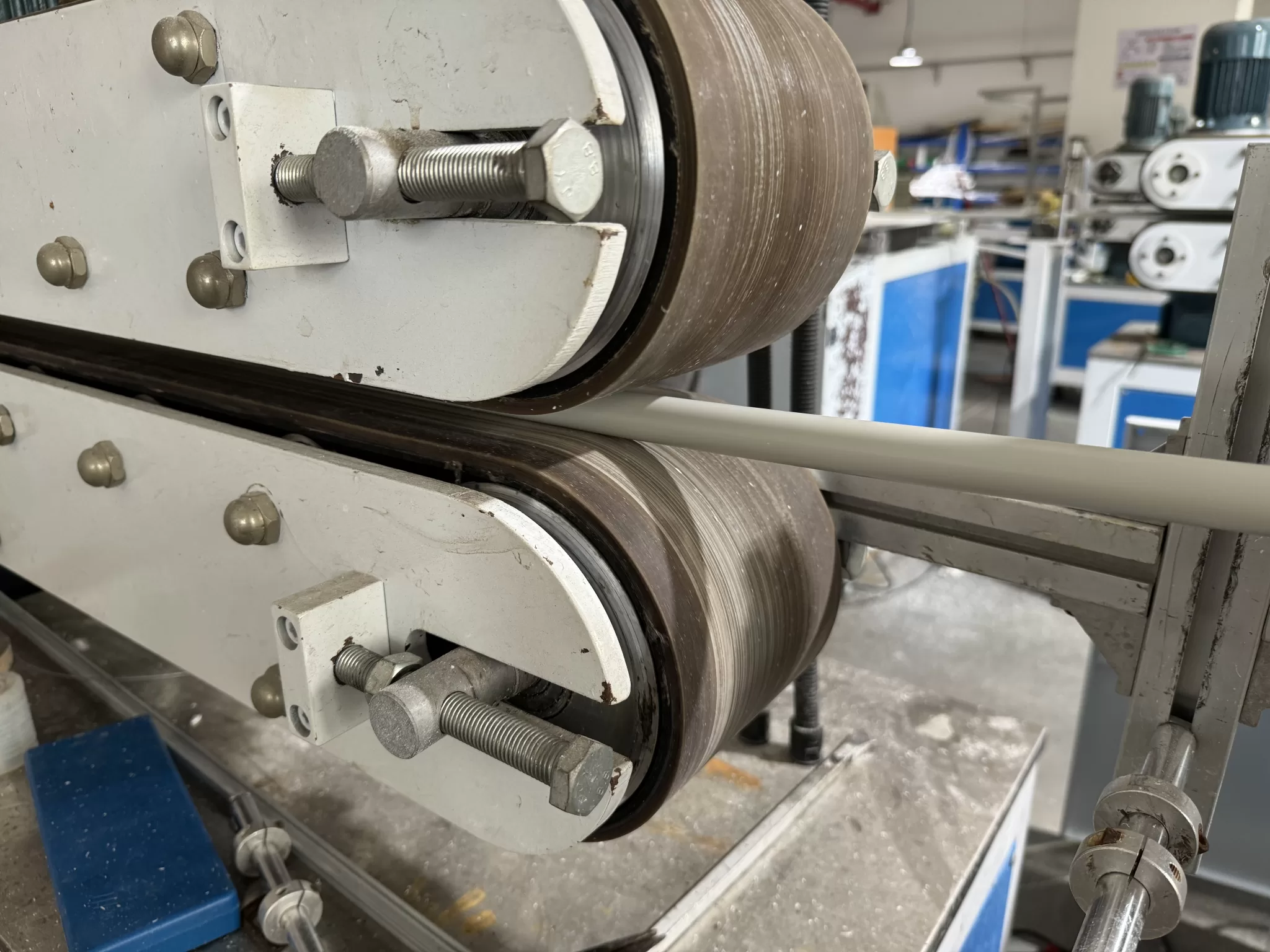
To maximize efficiency and product quality in plastic profile extrusion, consider the following best practices:
1. Choose the Right Material
Selecting the appropriate material is crucial for achieving the desired performance and durability of the extruded profile. Consider factors such as strength, flexibility, and resistance to environmental conditions.
2. Optimize Die Design
Invest in high-quality die design to ensure accurate shaping and reduce defects. A well-designed die can enhance flow characteristics and improve surface finish.
3. Monitor Temperature and Pressure
Maintaining consistent temperature and pressure throughout the extrusion process is essential. Use advanced sensors and controls to ensure optimal processing conditions.
4. Implement Quality Control
Regularly inspect extruded profiles for defects such as warping, discoloration, or dimensional inaccuracies. Implement a robust quality control system to identify and address issues promptly.
5. Train Your Team
Ensure that your team is well-trained in extrusion techniques and best practices. Continuous education and training can lead to improved efficiency and product quality.
Conclusion
Understanding plastic profile extrusion is essential for anyone involved in manufacturing or using extruded products. By recognizing the process, benefits, applications, and best practices, businesses can enhance their production capabilities and deliver high-quality products. Whether you’re in construction, automotive, or any other industry, embracing plastic profile extrusion can lead to innovative solutions and significant cost savings.
Frequently Asked Questions (FAQs)
What is the difference between extrusion and injection molding?
Extrusion produces continuous shapes, while injection molding creates discrete parts by injecting material into a mold.
Can recycled materials be used in plastic profile extrusion?
Yes, recycled materials can be used, making the process more sustainable and cost-effective.
What types of plastics are most commonly used in extrusion?
Commonly used plastics include PVC, polyethylene, and polystyrene, each offering different properties suited to various applications.