Plastic profiles are widely used in various industries due to their versatility, durability, and cost-effectiveness. However, like any material, they can fail if not handled or used correctly. Understanding the common reasons for plastic profile failure is crucial for ensuring product longevity and performance.
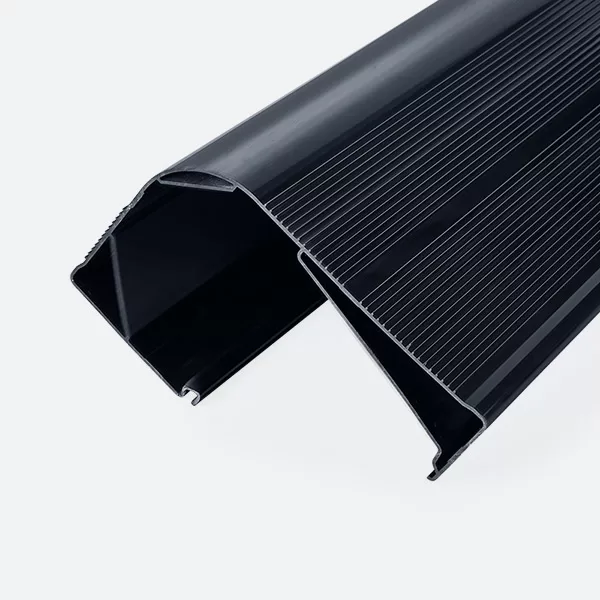
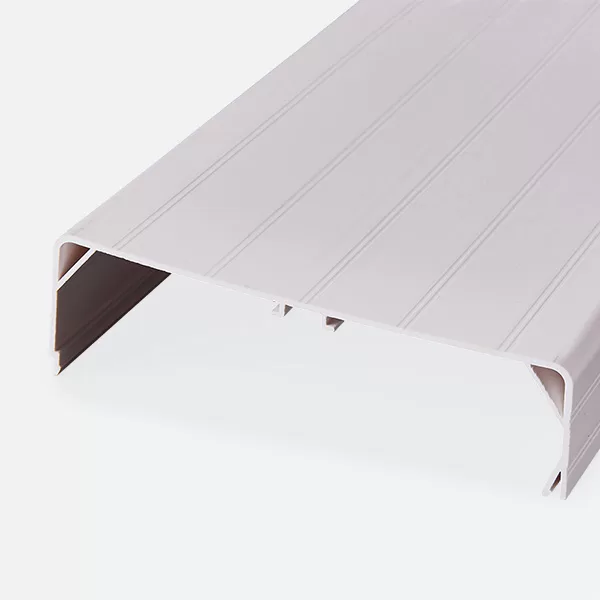
Key Factors Contributing to Plastic Profile Failure
- Material Selection:
- Incorrect Material Choice: Selecting a plastic extrusion material that is not suitable for the intended application can lead to premature failure. For example, using a brittle material in a high-impact environment can result in cracks or breakage.
- Lack of UV Resistance: Outdoor applications require materials that can withstand the harmful effects of sunlight. UV-resistant materials are essential to prevent degradation and discoloration.
- Design Flaws:
- Inadequate Fillet Radii: Sharp corners can create stress concentrations, leading to cracks and fractures. Proper fillet radii are crucial for distributing stress evenly.
- Overloading: Designing profiles to carry excessive loads can result in deformation or failure.
- Poor Mold Design: Mold defects, such as sink marks or warpage, can weaken the profile and contribute to failure.
- Manufacturing Issues:
- Molded-in Stress: Improper cooling or processing can result in internal stresses that can cause cracking or warping over time.
- Shrinkage Cavities: Insufficient material in specific areas can lead to voids or cavities that reduce strength.
- Weak Weld Lines: Poor weld lines, especially in complex profiles, can be points of weakness.
- Usage Conditions:
- Overloading: Exposing profiles to loads beyond their design limits can cause premature failure.
- Extreme Temperatures: Exposure to very high or low temperatures can affect the material’s properties and lead to cracking or deformation.
- Chemical Exposure: Contact with incompatible chemicals can cause degradation or corrosion.
Prevention Strategies
- Thorough Material Selection: Consider factors such as mechanical properties, chemical resistance, temperature tolerance, and UV resistance.
- Optimized Design: Ensure proper fillet radii, avoid sharp corners, and design profiles to withstand expected loads.
- Quality Manufacturing: Implement rigorous quality control measures to prevent defects like molded-in stress, shrinkage cavities, and weak weld lines.
- Proper Usage: Follow guidelines for load limits, temperature ranges, and chemical compatibility.
Conclusion
By understanding the common causes of plastic profile failure and implementing preventive measures, you can significantly improve the longevity and reliability of your products. Careful material selection, optimized design, quality manufacturing, and proper usage are essential for ensuring the success of plastic profiles in various applications.