Plastic extrusion processes have transformed the manufacturing world, offering versatility, efficiency, and cost-effectiveness. One particular method, Plastic Tri-Extrusion, has become increasingly popular due to its ability to create multi-layered, high-performance plastic products.
What is Plastic Tri-Extrusion?
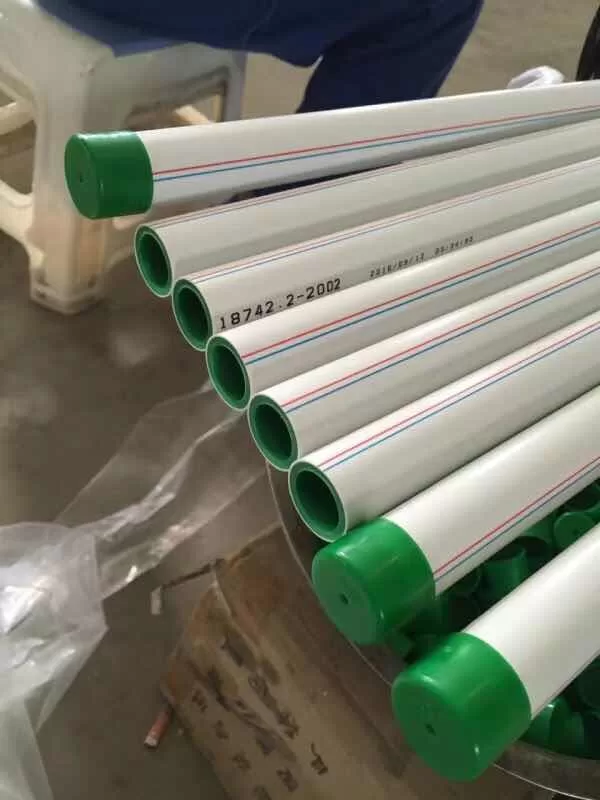
Plastic Tri-Extrusion is a manufacturing process where three different layers of plastic materials are extruded simultaneously. The process combines multiple polymers with different properties to create a single product with a unique set of characteristics. Unlike traditional single-layer extrusion, tri-extrusion allows manufacturers to optimize the performance, durability, and cost-efficiency of plastic parts by combining the best features of each polymer.
The Plastic Tri-Extrusion Process
In the Plastic Tri-Extrusion process, three separate extruders feed molten plastic into a common die. Each extruder processes a different type of polymer, which is carefully selected based on its properties such as flexibility, hardness, or resistance to environmental factors.
- Material Selection: Different materials are selected for the outer, middle, and inner layers. For example, the outer layer could offer UV resistance, the middle layer could provide strength, and the inner layer could ensure flexibility.
- Extrusion: The materials are heated to their melting points in separate extruders, then combined as they flow through a common die to form a single, multi-layered product.
- Cooling and Shaping: The extruded product is then cooled and shaped into its final form, whether it’s tubing, sheeting, or other profiles.
Benefits of Plastic Tri-Extrusion
Plastic Tri-Extrusion offers numerous advantages over single or dual extrusion processes, making it a go-to choice for industries requiring advanced plastic components.
1. Customization
One of the biggest benefits of tri-extrusion is the ability to customize products by combining different types of materials. This allows manufacturers to tailor products to meet specific requirements like enhanced flexibility, higher strength, or superior environmental resistance.
2. Cost-Efficiency
By using lower-cost materials in non-critical layers (such as the core layer), while reserving higher-quality materials for outer layers, Plastic Tri-Extrusion can help reduce overall material costs without compromising product performance.
3. Enhanced Durability
The combination of different layers provides greater durability. The outer layers can protect against wear and tear, UV radiation, or chemical exposure, while the core layers maintain the product’s structural integrity.
4. Improved Performance
Tri-extruded products can exhibit enhanced performance characteristics that single-layer products cannot achieve. These can include higher heat resistance, better impact absorption, or improved sealing properties.
Applications of Plastic Tri-Extrusion
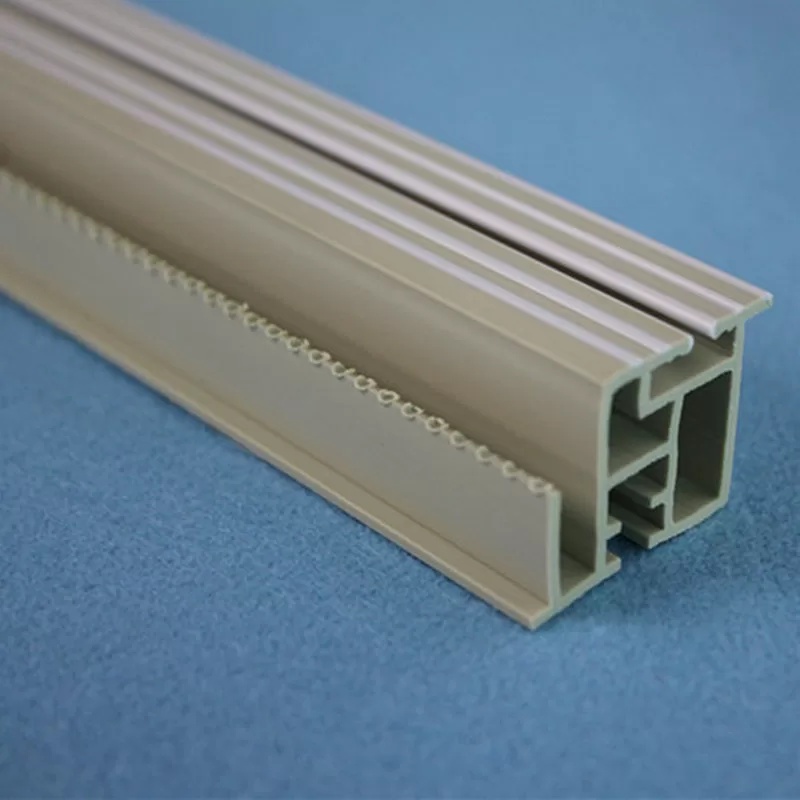
Plastic Tri-Extrusion is widely used across various industries due to its flexibility and ability to create complex, multi-layered products.
1. Automotive Industry
In the automotive industry, tri-extrusion is often used to manufacture weatherstripping, seals, and gaskets that require multiple layers for enhanced sealing performance, durability, and UV resistance.
2. Construction Industry
For construction materials like window profiles, trim, and siding, tri-extrusion enables the creation of products that combine strength, UV resistance, and insulation properties.
3. Medical Devices
Medical-grade plastic tubing, catheters, and other healthcare-related products benefit from tri-extrusion due to its ability to create products that are both durable and biocompatible, while offering resistance to various chemicals.
4. Packaging Industry
In the packaging industry, tri-extrusion is used to produce multi-layer films and containers that offer improved barrier protection against moisture, oxygen, and other environmental factors.
Materials Used in Plastic Tri-Extrusion
The materials used in Plastic Tri-Extrusion can vary widely depending on the application, but common polymers include:
- Polyvinyl Chloride (PVC): Often used for durability and flexibility.
- Polypropylene (PP): Known for chemical resistance and low cost.
- Polyethylene (PE): Offers high flexibility and impact resistance.
- Thermoplastic Elastomers (TPE): Used for flexibility and soft-touch applications.
Challenges in Plastic Tri-Extrusion
While Plastic Tri-Extrusion offers numerous advantages, there are also some challenges involved.
1. Complex Setup
The setup for tri-extrusion requires precise control of each extruder and the die. This makes the initial setup process more complex compared to traditional extrusion.
2. Material Compatibility
Ensuring that the three materials bond properly during the extrusion process can be tricky. Incompatible materials can result in weak layers or product failure.
3. Higher Initial Costs
The machinery and tooling for tri-extrusion are more expensive than for single-layer extrusion. However, the long-term benefits, such as reduced material costs and increased product performance, often offset these initial investments.
Conclusion
Plastic Tri-Extrusion is a highly versatile and efficient manufacturing process that enables the production of multi-layered plastic products with superior performance. Its ability to combine different polymers into a single product makes it ideal for industries requiring advanced material properties, such as automotive, medical, and construction sectors. Though there are challenges in setup and material compatibility, the benefits of customization, durability, and cost-efficiency make Plastic Tri-Extrusion an essential technology in modern manufacturing.
FAQs
1. What is the main advantage of Plastic Tri-Extrusion over single-layer extrusion?
The main advantage is the ability to combine multiple materials into a single product, offering superior performance, customization, and cost-efficiency.
2. Which industries benefit the most from Plastic Tri-Extrusion?
Industries such as automotive, construction, medical, and packaging see the most significant benefits from this process.
3. Can any polymer be used in the Tri-Extrusion process?
While many polymers can be used, compatibility between the materials is essential to ensure proper bonding and product performance.