Polypropylene (PP) is a widely used thermoplastic polymer derived from the polymerization of propylene. Known for its excellent performance and cost-effectiveness, PP plastic profiles have become a popular choice across various industries.
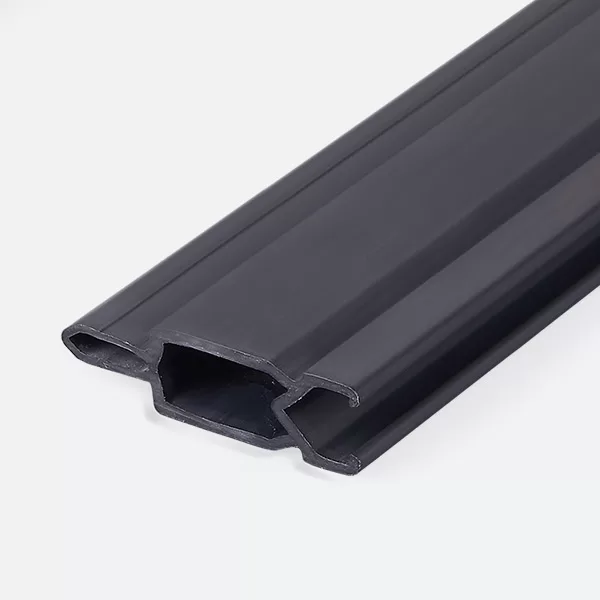
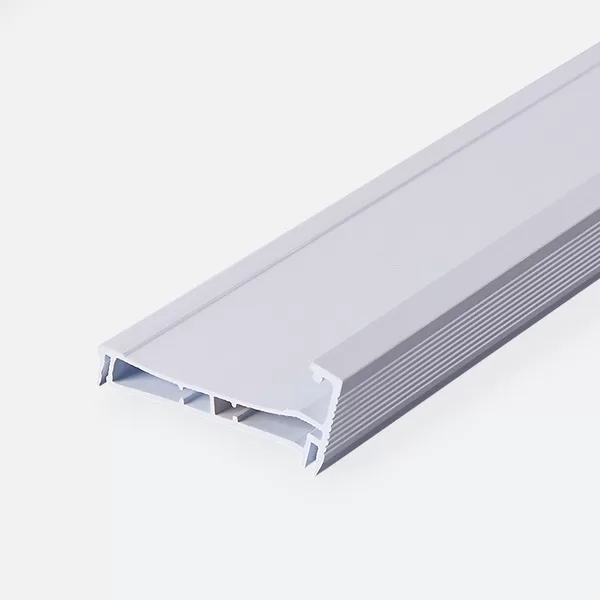
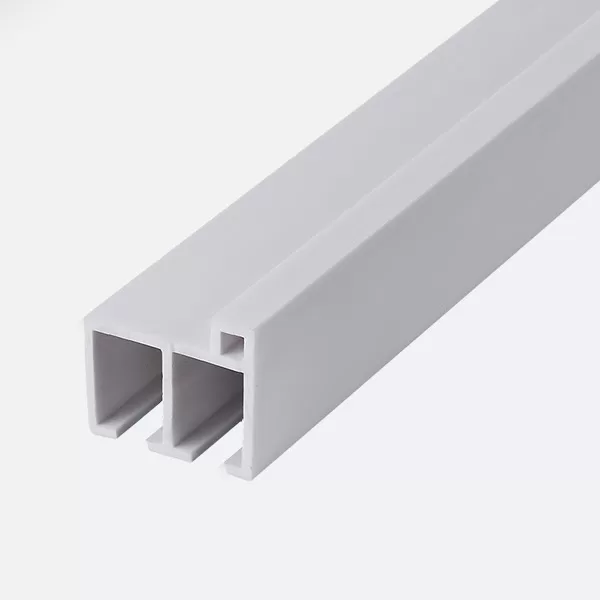
What Are PP Plastic Profiles?
PP plastic profiles are formed from polypropylene, a lightweight polymer characterized by its versatility and durability. They are used extensively due to their easy processing capabilities and affordability. However, they do have certain limitations, such as low-temperature toughness and susceptibility to aging. Recent advancements in modified polypropylene products have improved these weaknesses, expanding their usability in various applications.
Key Properties of PP Plastic Profiles
- Chemical and Physical Properties:
- Density: Approximately 0.91 g/cm³, making it lightweight.
- Melting Temperature: About 174°C, providing good thermal stability.
- Strength and Hardness: High strength, wear resistance, and good chemical corrosion resistance.
- Heat Resistance: Can withstand temperatures up to 120°C without losing performance.
- Bending Fatigue Resistance: Excellent resistance to bending fatigue, capable of enduring hundreds of thousands of cycles.
Production Methods for PP Plastic Profiles
There are several industrial methods for producing PP plastic profiles, including:
- Solvent Method: The most commonly used method.
- Liquid Phase Bulk Method: Another effective production technique.
- Gas Phase Bulk Method: Used for large-scale production.
- Solution Method: Less common but still utilized.
Types of PP Plastic Profiles
PP plastic profiles can be classified based on the composition of monomers used in polymerization:
- Homopolymer Grade: Made from a single propylene monomer, offering higher crystallinity and mechanical strength.
- Copolymer Grade: Created by introducing a small amount of ethylene monomer during polymerization. It can be further divided into:
- Block Copolymer Polypropylene: Offers high impact strength.
- Random Copolymer Polypropylene: Provides improved transparency and impact resistance.
Advantages of PP Plastic Profiles Over Other Thermoplastics
PP plastic profiles offer several advantages compared to other general thermoplastics:
- Low Specific Gravity: Lightweight and easy to handle.
- Good Rigidity: Maintains shape under stress.
- High Strength: Suitable for demanding applications.
- Heat Resistance: Can endure temperatures above 100°C.
- Chemical Corrosion Resistance: Ideal for various industrial environments.
Limitations of PP Plastic Profiles
Despite their advantages, PP plastic profiles have some drawbacks:
- Poor Low-Temperature Impact Resistance: May become brittle in cold conditions.
- Easy Aging: Can degrade over time if not properly stabilized.
- Large Molding Shrinkage: Requires careful consideration during the manufacturing process.
Modifying PP Plastic Profiles
To enhance the performance of polypropylene, various modification techniques can be employed:
- Blending and Filling: Adding materials like calcium carbonate or talcum powder can improve hardness and dimensional stability.
- Reinforcement: Incorporating glass fibers or other materials increases tensile strength and impact resistance.
- Additives: Special additives can provide weather resistance, flame retardancy, conductivity, and more.
Processing Techniques for PP Plastic Profiles
PP plastic profiles can be manufactured using multiple processing methods, including:
- Injection Molding: Ideal for creating complex industrial parts and appliances.
- Extrusion: Produces pipes, sheets, and profiles for various applications.
- Blow Molding: Used for small containers and bottles.
- Thermoforming: Enables the creation of custom shapes and sizes.
- Rotational Molding: Suitable for large chemical storage tanks and containers.
Applications of PP Plastic Profiles
PP plastic profiles find extensive use across diverse industries due to their adaptability and cost-effectiveness. Common applications include:
- Industrial Parts: Components for machinery and equipment.
- Building Materials: Used in construction for durability and aesthetic appeal.
- Consumer Goods: Everyday items such as containers, utensils, and storage solutions.
- Packaging: High-strength films and flexible packaging solutions.
Conclusion
In conclusion, PP plastic profiles are a versatile and cost-effective option among thermoplastic materials. Their lightweight nature, excellent mechanical properties, and adaptability to various production methods make them suitable for a wide range of applications. While they do have limitations, ongoing modifications and technological advancements continue to enhance their performance, ensuring that PP plastic profiles remain a top choice in the building materials and manufacturing industries. If you’re considering options for your next project, PP plastic profiles are definitely worth exploring.