Discover the exceptional features of PVC plastic profiles, including rainproofing, fire resistance, anti-static properties, and ease of shaping, alongside its cost-effective manufacturing process for high productivity. Let’s explore why PVC excels in these aspects, starting from its production process.
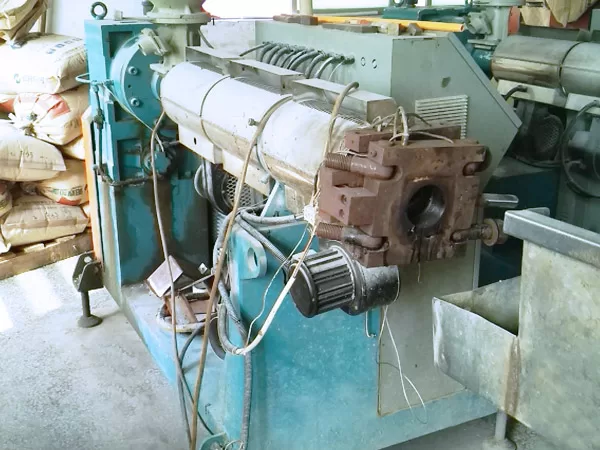
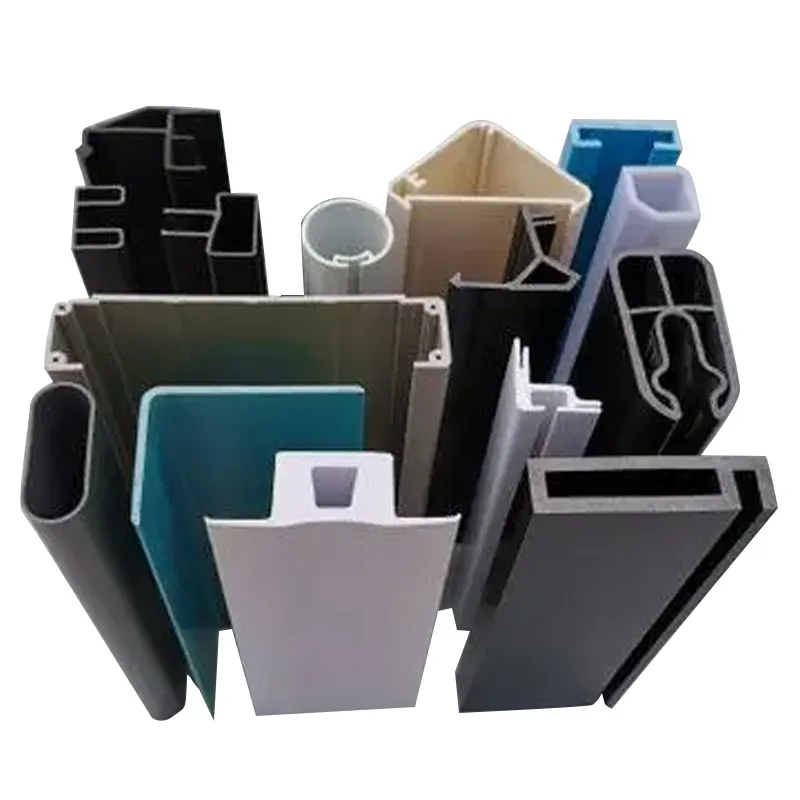
The production of PVC profiles involves a simple process utilizing essential equipment like a roller press, printing unit, back coating machine, and cutter to create thin films ranging from 0.3MM to 0.7MM in thickness. An important aspect often overlooked is the back coating, which plays a critical role in ensuring the top-notch performance of PVC films. Comprised of special materials, the back coating acts as a high-energy affinity agent, allowing PVC films to adhere securely to various surfaces without delamination for extended periods, up to ten or even fifteen years. Through a production method conducted at high temperatures, up to 220 degrees in the rolling machine, PVC films gain exceptional light and fire resistance qualities, ensuring premium product excellence. While the production machinery demands a substantial investment, the straightforward production process and high output make PVC a low-input, high-output solution overall.
Addressing PVC Profile Deformation Challenges
Internal stress in PVC profiles can lead to bending, cracks, or deformation, impacting both mechanical properties and overall quality.
Causes of Internal Stress in Profiles:
- Uneven orientation stresses during molding
- Variations in cooling shrinkage
- Unequal wall thickness and cooling rates
Solutions:
- Optimize extrusion temperature and pressure
- Ensure uniform wall thickness for consistent cooling
- Regulate extrusion speed for minimal stress deformities
Dealing with Profile Bending Issues
Profile bending exceeding standards can result from misalignment in production processes and inconsistencies in force application.
Causes of Bending:
- Misalignment in production line components
- Uneven force application on profile surfaces
- Improper storage leading to deformation
Remedies:
- Align production line components accurately
- Adjust force application for uniform traction
- Store profiles appropriately to prevent deformation
Resolving Bubbles, Cracks, and Pitting in PVC Profiles
Defects such as bubbles, cracks, and pitting indicate material impurities, thermal instability, and inadequate extrusion processes.
Root Causes:
- Excess moisture and volatiles in materials
- Poor thermal stability of PVC
- Inefficient extruder exhaust system
Solutions:
- Manage raw material impurities effectively
- Optimize temperature and pressure settings during extrusion
- Ensure proper functioning of the extruder exhaust system
Implementing effective solutions tailored to each issue can significantly enhance the quality and durability of PVC plastic profiles, ensuring optimal performance and customer satisfaction.